A Method for Machining Stepped Hole from Small Hole End
A stepped hole and hole end technology, applied in boring/drilling, metal processing equipment, drilling/drilling equipment, etc., can solve the problems of impacting the tool holder, difficult to ensure coaxiality, and inability to process, and achieves guaranteed Dimensional accuracy and machining depth, avoiding tool holder breakage, and ensuring the effect of coaxiality
- Summary
- Abstract
- Description
- Claims
- Application Information
AI Technical Summary
Problems solved by technology
Method used
Image
Examples
Embodiment Construction
[0046] A method for processing a stepped hole from a small hole end provided by an embodiment of the present invention includes the following steps:
[0047] 1) Parts clamping and tooling: Align the parts and fix them on the console, so that the small diameter end of the stepped hole to be processed on the part faces the direction of the main shaft of the processing equipment, and the centerline of the small diameter of the stepped hole is aligned with the equipment The axis of the spindle. When machining the small hole of the stepped hole, the drill bit and the boring tool (or reamer) are respectively clamped on the equipment spindle, and the reverse countersink is clamped on the equipment spindle when machining the stepped hole with a larger diameter on the other side of the stepped hole . see figure 2 and image 3 , the reverse spot facing tool 1 includes a handle 11 , a tool body 12 , a tool holder 13 and a blade 14 . Wherein, one end of the handle 11 is connected wit...
PUM
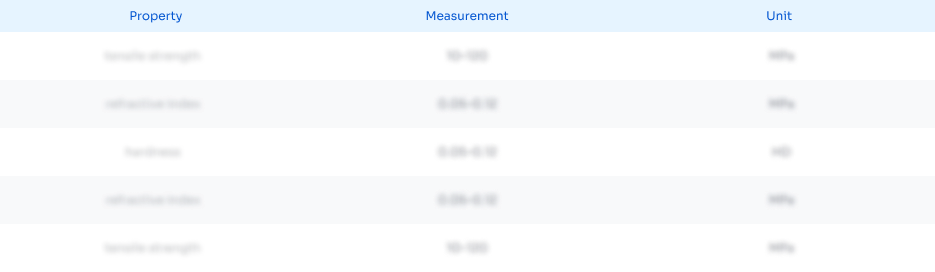
Abstract
Description
Claims
Application Information

- R&D Engineer
- R&D Manager
- IP Professional
- Industry Leading Data Capabilities
- Powerful AI technology
- Patent DNA Extraction
Browse by: Latest US Patents, China's latest patents, Technical Efficacy Thesaurus, Application Domain, Technology Topic, Popular Technical Reports.
© 2024 PatSnap. All rights reserved.Legal|Privacy policy|Modern Slavery Act Transparency Statement|Sitemap|About US| Contact US: help@patsnap.com