Preparation method of acetylene method vinyl acetate catalyst
A technology of vinyl acetate and catalyst, which is applied in the field of preparation of vinyl acetate catalyst by acetylene method, can solve the problems of poor catalyst stability and short service life, and achieve the effect of improving stability and service life and good technical effect
- Summary
- Abstract
- Description
- Claims
- Application Information
AI Technical Summary
Problems solved by technology
Method used
Image
Examples
Embodiment 1
[0053] (1) Activated carbon heat treatment: 300ml coconut shell activated carbon AC is placed in a tubular atmosphere furnace, 2 and N 2 Mixed atmosphere (O in the mixed atmosphere 2 The volume is 5%), the temperature is programmed to 400°C (the heating rate is 10°C / min, the mixed gas flow rate is 30ml / min), after constant temperature for 3h, it is naturally cooled to room temperature, and the modified carbon AC1 is obtained;
[0054] (2) Ionic liquid treatment: Take 100ml of 5.0g / L ethanol solution of N-ethyl acetate pyridinium acetate ionic liquid ([EtaPy]Ac), mix with 100ml of modified carbon AC1, soak at 25°C for 6h, After filtration, dry in vacuum (vacuum pressure: 100Pa) at 40°C for 24 hours to obtain the finished modified carbon product AC2;
[0055] (3) Catalyst preparation
[0056] Preparation of dipping solution: weigh 20.0g of zinc acetate (molecular formula: Zn(CH 3 COO) 2 ) was dissolved in deionized water, and acetic acid was used to adjust its pH value to 4...
Embodiment 2
[0071] (1) Activated carbon heat treatment: 300ml coconut shell activated carbon AC is placed in a tubular atmosphere furnace, 2 and N 2 Mixed atmosphere (O in the mixed atmosphere 2 The volume is 5%), the temperature is programmed to 400°C (the heating rate is 10°C / min, the mixed gas flow rate is 30ml / min), after constant temperature for 3h, it is naturally cooled to room temperature, and the modified carbon AC1 is obtained;
[0072] (2) Ionic liquid treatment: take 100ml of 5.0g / L ethanol solution of N-acetoxypyridinium acetate ionic liquid ([EtPy]Ac), mix with 100ml of modified carbon AC1, soak at 25°C for 6h, and filter Dry in vacuum (vacuum pressure: 100Pa) at 40°C for 24 hours to obtain the finished modified carbon product AC2;
[0073] (3) Catalyst preparation
[0074] Preparation of dipping solution: weigh 20.0g of zinc acetate (molecular formula: Zn(CH 3 COO) 2 ) was dissolved in deionized water, and acetic acid was used to adjust its pH value to 4.70 to obtain 2...
Embodiment 3
[0089] (1) Activated carbon heat treatment: 300ml coconut shell activated carbon AC is placed in a tubular atmosphere furnace, 3 and N 2 Mixed atmosphere (O in the mixed atmosphere 3 Under the condition of 5% volume), the temperature was programmed to 400°C (the heating rate was 10°C / min, the flow rate of the mixed gas was 30ml / min), and after constant temperature for 3 hours, it was naturally cooled to room temperature to obtain modified carbon AC1;
[0090] (2) Ionic liquid treatment: Take 100ml of 5.0g / L ethanol solution of N-(2-hydroxy-3-chloropropyl)pyridine acetate ionic liquid ([HPy]Ac) and mix it with 100ml modified carbon AC1 , impregnated at 25°C for 6h, filtered and dried at 40°C in vacuum (vacuum pressure: 100Pa) for 24h to obtain the finished modified carbon product AC2;
[0091] (3) Catalyst preparation
[0092] Preparation of dipping solution: weigh 20.0g of zinc acetate (molecular formula: Zn(CH 3 COO) 2 ) was dissolved in deionized water, and acetic acid ...
PUM
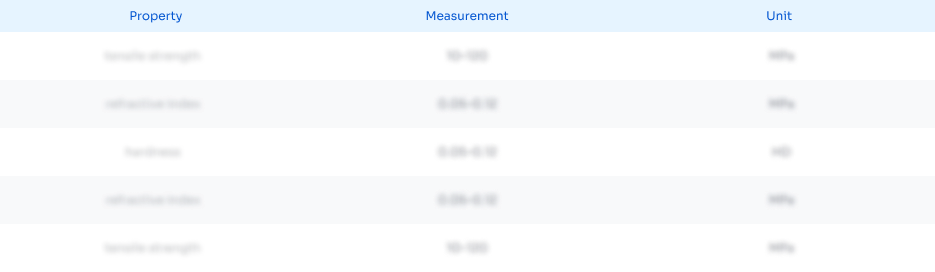
Abstract
Description
Claims
Application Information

- R&D Engineer
- R&D Manager
- IP Professional
- Industry Leading Data Capabilities
- Powerful AI technology
- Patent DNA Extraction
Browse by: Latest US Patents, China's latest patents, Technical Efficacy Thesaurus, Application Domain, Technology Topic, Popular Technical Reports.
© 2024 PatSnap. All rights reserved.Legal|Privacy policy|Modern Slavery Act Transparency Statement|Sitemap|About US| Contact US: help@patsnap.com