Method for preparing rubber filler by taking coal gasification slag as raw material
A technology of coal gasification slag and rubber filler, applied in chemical instruments and methods, fibrous filler, chemical industry, etc., can solve the problems of less than 50% comprehensive utilization of gasification slag, large stock of gasification slag, heavy environmental burden, etc. , to achieve the effect of saving natural mineral resources, good matrix affinity and good dispersibility
- Summary
- Abstract
- Description
- Claims
- Application Information
AI Technical Summary
Problems solved by technology
Method used
Image
Examples
Embodiment 1
[0027] see figure 1 , a kind of method that takes coal gasification slag as raw material to prepare rubber filler, has following steps:
[0028] (1), raw material pretreatment
[0029] Raw material pretreatment includes drying stage, magnetic separation stage, and activation stage. According to the physical and chemical properties of coal gasification slag raw materials, the sequence and combination of drying stage, magnetic separation stage, and activation stage can be freely adjusted; the drying stage is used to remove gas The moisture in the slag raw material should be controlled below 0.8%. The magnetic separation stage is used to control the content of heavy metals in the coal gasification slag. The activation stage uses an activator to activate the residual carbon in the coal gasification slag at high temperature to increase its surface area and surface activity;
[0030] (2), ultra-fine processing
[0031] Carrying out crushing and grading treatment on the coal gasif...
Embodiment 2
[0044] The coal gasification slag from a company in Lu'an, Shanxi has a residual carbon content of 15.3%, iron oxide content of 3.6%, manganese oxide content of 4%, and a moisture content of 4%. The proposed pretreatment process is drying, magnetic separation and activation. First, use a rotary kiln to dry the material, set the temperature at the kiln head to 320°C, set the temperature at the kiln tail to 130°C, and dry to a moisture content of 0.3%; use a dry magnetic separator to magnetically separate once at a magnetic field strength of 1.5T; Using a tubular resistance furnace at 900°C, activate with water vapor as the activator for 30 minutes; then feed the activated material into the steam kinetic energy mill with a screw feeder, use 0.7MPa, superheated steam at 290°C, and use the speed setting A 1500rpm classifier is used to ultrafinely pulverize the material; the modifier uses silane coupling agent (KH570) accounting for 0.3% of the total material, sodium stearate accoun...
Embodiment 3
[0048] The coal gasification slag from a company in Yulin, Shaanxi, has a residual carbon content of 26.3%, an iron oxide content of 4.6%, manganese oxide was not detected, and a moisture content of 7%. The proposed pretreatment process is fluidized bed drying, magnetic separation and activation. First, use a fluidized bed dryer to dry the material, set the inlet temperature to 280°C, set the outlet temperature to 115°C, and dry to a moisture content of 0.5%; use a dry magnetic separator to magnetically separate once at a magnetic field strength of 2.0T ;Use a tubular resistance furnace at 850°C to activate with water vapor and carbon dioxide as activators for 45 minutes; then feed the activated material into the jet mill with a screw feeder, use 1.2MPa compressed air, and use a rotating speed of 2900rpm The classifier carries out superfine pulverization of the material; among them, the modifier adopts silane coupling agent (NXT) accounting for 0.5% of the total material and po...
PUM
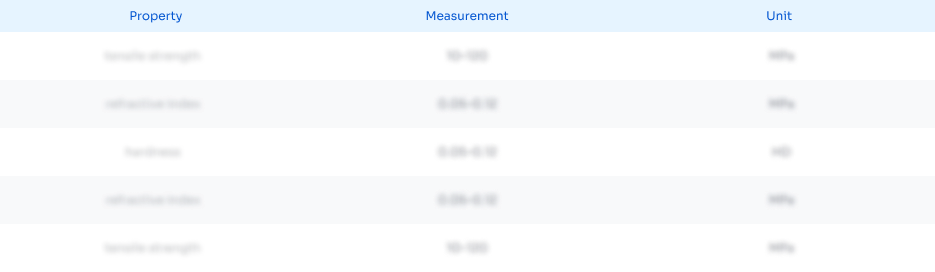
Abstract
Description
Claims
Application Information

- R&D Engineer
- R&D Manager
- IP Professional
- Industry Leading Data Capabilities
- Powerful AI technology
- Patent DNA Extraction
Browse by: Latest US Patents, China's latest patents, Technical Efficacy Thesaurus, Application Domain, Technology Topic, Popular Technical Reports.
© 2024 PatSnap. All rights reserved.Legal|Privacy policy|Modern Slavery Act Transparency Statement|Sitemap|About US| Contact US: help@patsnap.com