Butt welding assembly method for stainless steel tubes
A technology of stainless steel pipe and assembly method, which is applied in the direction of welding/welding/cutting articles, auxiliary devices, welding equipment, etc., can solve the problems of low efficiency, large consumption of argon gas, and difficult control of welding size, and achieve low precision requirements, The effect of reducing the amount of argon used and reducing the cost of use
- Summary
- Abstract
- Description
- Claims
- Application Information
AI Technical Summary
Problems solved by technology
Method used
Image
Examples
Embodiment Construction
[0025] The present invention will be described in detail below in conjunction with the accompanying drawings. All equivalent changes and modifications made according to the contents of this specification should belong to the technical scope of the application of the present invention.
[0026] The present invention is used for the butt weld assembly of stainless steel pipes. Several triangular inserts are placed in the butt welds between the circumferences of the stainless steel pipes, and the depth of the triangular inserts inserted into the butt welds is controlled to control the The size of the weld gap between the stainless steel pipes is kept consistent along the circumferential direction, and the spot welding is positioned at the contact position.
[0027] Please refer to figure 1 , image 3 and Figure 4 , the triangular inlay 2 is made of the same material as the stainless steel pipe 1, and the thickness, size and angle of the triangular inlay 2 are determined accord...
PUM
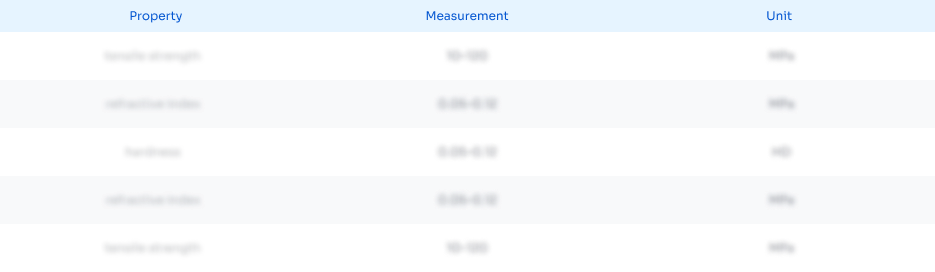
Abstract
Description
Claims
Application Information

- R&D Engineer
- R&D Manager
- IP Professional
- Industry Leading Data Capabilities
- Powerful AI technology
- Patent DNA Extraction
Browse by: Latest US Patents, China's latest patents, Technical Efficacy Thesaurus, Application Domain, Technology Topic, Popular Technical Reports.
© 2024 PatSnap. All rights reserved.Legal|Privacy policy|Modern Slavery Act Transparency Statement|Sitemap|About US| Contact US: help@patsnap.com