Nonionic-cationic copolymer containing polyether branched chain and preparation method thereof
A cationic copolymer, non-ionic technology, applied in separation methods, chemical dehydration/demulsification, liquid separation, etc., can solve the problems of sludge clogging water treatment facilities, short residence time, slow dispersion rate, etc. Good, fast dehydration rate, less use effect
- Summary
- Abstract
- Description
- Claims
- Application Information
AI Technical Summary
Problems solved by technology
Method used
Image
Examples
Embodiment 1
[0019] Add 15.0g of maleic anhydride and 100.0g of polyether AE121 obtained by polyaddition reaction of organic amine compounds with propylene oxide and ethylene oxide into a three-necked flask equipped with stirring, reflux and condensing devices, and slowly heat to 60°C , start stirring, continue heating to 90°C for 2 hours, then add 25.0g of 60% diallyldimethylammonium chloride aqueous solution and 380.0g of deionized water, control the temperature between 75°C and 80°C, drop Add a solution of 0.9g ammonium persulfate dissolved in 10.0g deionized water to initiate polymerization; after adding the initiator dropwise, raise the temperature to 80°C-85°C and continue the reaction for 3.5h to obtain a viscous liquid with a solid content of about 25%. (AE121MC1).
Embodiment 2
[0021] Add 5.0g of maleic anhydride and 100.0g of polyether SP169 obtained by polyaddition reaction of stearyl alcohol with propylene oxide and ethylene oxide into a three-necked flask equipped with stirring, reflux and condensing devices, and slowly heat to 60°C , start stirring, continue heating to 90°C for 2 hours, then add 6.25g of 80% acryloyloxyethyltrimethylammonium chloride aqueous solution and 293.75g of deionized water, and control the temperature between 75°C and 80°C. Add dropwise a solution of 0.015g of sodium persulfate dissolved in 5.0g of deionized water to initiate polymerization; after adding the initiator, raise the temperature to 80°C to 85°C and continue the reaction for 3.5h to obtain a viscous liquid with a solid content of about 27%. (SP169MC1).
Embodiment 3
[0023] In the 7-square enamel reaction kettle, add 1000Kg of polyether SP169 obtained by the polyaddition reaction of octadecyl alcohol, propylene oxide and ethylene oxide, start heating, start stirring when the temperature rises to 60°C, and add 80Kg maleic anhydride, continue to heat to 90°C and keep it warm for 4 hours, then add 200Kg concentration of 60% diallyldimethylammonium chloride aqueous solution and 3300Kg deionized water, control the temperature between 75°C and 80°C, Add dropwise a solution of 0.4Kg ammonium persulfate dissolved in 10Kg deionized water to initiate polymerization; after adding the initiator, raise the temperature to 80°C to 85°C and continue the reaction for 5 hours to obtain a viscous liquid with a solid content of about 26% (SP169MC2 ).
PUM
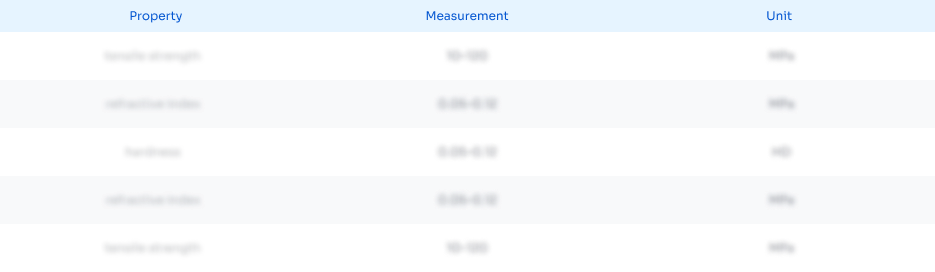
Abstract
Description
Claims
Application Information

- R&D
- Intellectual Property
- Life Sciences
- Materials
- Tech Scout
- Unparalleled Data Quality
- Higher Quality Content
- 60% Fewer Hallucinations
Browse by: Latest US Patents, China's latest patents, Technical Efficacy Thesaurus, Application Domain, Technology Topic, Popular Technical Reports.
© 2025 PatSnap. All rights reserved.Legal|Privacy policy|Modern Slavery Act Transparency Statement|Sitemap|About US| Contact US: help@patsnap.com