Physical expansion foaming microsphere coated with diisopropyl azodicarboxylate and preparation method thereof
A technology for wrapping diisopropyl azodicarboxylate and diisopropyl azodicarboxylate, which is applied in the field of physically expanded foamed microspheres and its preparation, and can solve problems such as thermal runaway, poor compatibility, and danger , to improve the stability of the
- Summary
- Abstract
- Description
- Claims
- Application Information
AI Technical Summary
Problems solved by technology
Method used
Image
Examples
Embodiment 1
[0029] The raw material composition formula of microsphere is as follows: methyl methacrylate: 14g; Phenyl methacrylate: 4g; Diisopropyl azodicarboxylate: 7g; Azobisisoheptanonitrile: 400mg; ) peroxydicarbonate: 450 mg; 1,4-butylene glycol dimethacrylate: 0.055 g. Deionized water: 112ml; polyvinyl alcohol 1788: 0.56g; sodium chloride: 5.6g.
[0030] According to above-mentioned formula, prepare according to the following method:
[0031] (1) Get methyl methacrylate, phenyl methacrylate, diisopropyl azodicarboxylate, initiator azobisisoheptanonitrile and two (tert-butylcyclohexane) peroxydicarbonate, crosslinking agent 1,4-Butanediol Dimethacrylate, fully stirred and mixed to obtain an oil phase solution. Nitrogen gas was bubbled into the oil phase solution to remove oxygen for 10 minutes.
[0032] (2) Take deionized water, polyvinyl alcohol 1788, and sodium chloride, stir and mix well to make an aqueous phase solution. Nitrogen was blown into the aqueous phase solution to ...
Embodiment 2
[0037] The preparation method is the same as in Example 1. The raw material composition formula of the microspheres is as follows: methyl methacrylate: 14g; phenyl methacrylate: 2g; diisopropyl azodicarboxylate: 10g; azobisisoheptanonitrile: 850mg; 3-Butanediol ester: 0.014 g. Deionized water: 112mL; polyvinyl alcohol 1788: 0.56g; sodium chloride: 5.6g.
[0038] The characterization results showed that the average particle size of the microsphere product produced by the reaction was 247±30 μm. The initial expansion temperature of the microspheres is 172°C, the concentrated foaming temperature is 188°C, and the foaming rupture temperature is 220°C. The expansion ratio of the microspheres is 7.8 times. The appearance of microspheres before and after expansion under the microscope is as follows: figure 2 shown.
Embodiment 3
[0040] The preparation method is the same as in Example 1. The raw material composition formula of microspheres is as follows: methyl methacrylate: 14g; 850mg; 1,4-Butanediol dimethacrylate: 0.01g; 1,3-Butanediol dimethacrylate: 0.03g. Deionized water: 112mL; polyvinyl alcohol 1788: 0.56g; sodium chloride: 5.6g.
[0041]The characterization results showed that the average particle size of the microsphere product produced by the reaction was 510±92 μm. The initial expansion temperature of the microspheres is 170°C, the concentrated foaming temperature is 180°C, and the foaming rupture temperature is 210°C. The foaming expansion ratio of the microspheres is 10.2 times. The appearance of microspheres before and after expansion under the microscope is as follows: image 3 shown.
PUM
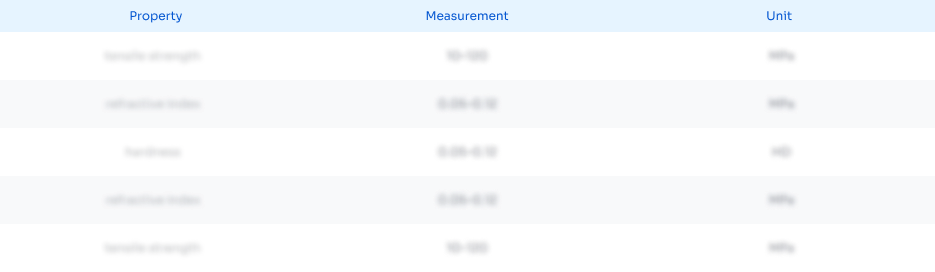
Abstract
Description
Claims
Application Information

- R&D
- Intellectual Property
- Life Sciences
- Materials
- Tech Scout
- Unparalleled Data Quality
- Higher Quality Content
- 60% Fewer Hallucinations
Browse by: Latest US Patents, China's latest patents, Technical Efficacy Thesaurus, Application Domain, Technology Topic, Popular Technical Reports.
© 2025 PatSnap. All rights reserved.Legal|Privacy policy|Modern Slavery Act Transparency Statement|Sitemap|About US| Contact US: help@patsnap.com