Mining high-water high-strength filling material and preparation method thereof
A filling material and high-strength technology, applied in the field of mining materials, can solve the problems of high cost of filling materials, cumbersome construction procedures, high compressive strength, avoid environmental pollution and health hazards of construction workers, reduce condensation time, The effect of high compressive strength
- Summary
- Abstract
- Description
- Claims
- Application Information
AI Technical Summary
Problems solved by technology
Method used
Image
Examples
preparation example Construction
[0025] A method for preparing a high-water and high-strength filling material for mines is specifically as follows: the raw materials of the A component and the B component are mixed in proportion, stirred evenly, packaged and stored separately, and the filling material is obtained.
[0026] Correspondingly, the present invention also provides the preparation method of described composite additive:
[0027] (1) 20-70 parts of aluminum sulfate, 2-10 parts of sodium metaaluminate, and 2-10 parts of limestone are mixed and ball-milled to an average particle size of 40 μm powder,
[0028] (2) Add 5-20 parts of alkanolamine to the reactor, stir the powder in (1) and heat it in a water bath until uniform, the heating temperature is 50-60°C, then cool to room temperature, add 2-10 parts of dispersant Continue to stir evenly
Embodiment 1
[0031] Mix and ball mill 60 parts of aluminum sulfate, 10 parts of sodium metaaluminate, and 8 parts of limestone to 40 μm powder for later use, add 20 parts of triethanolamine to the reaction kettle, mix and stir the prepared powder at 50°C, cool to room temperature, add 2 parts of hydroxypropyl methylcellulose were stirred evenly to obtain a composite additive.
[0032] Then, use the above-mentioned product composite additives to prepare mining high-water and high-strength filling materials:
[0033] Weigh A component by mass: 63 parts of sulfoaluminate cement, 10 parts of fly ash, 5 parts of sodium bentonite, 1 part of sodium gluconate, 1 part of magnesium aluminum silicate; B component: hemihydrate gypsum 5 parts, quicklime 2 parts, kaolin 5 parts, quartz powder 5 parts, composite additive 3 parts.
[0034] The raw materials in the above-mentioned components A and B are mixed in proportion and stirred evenly to obtain the A material and the B material of the filling mater...
Embodiment 2
[0038] Mix and ball mill 70 parts of aluminum sulfate, 3 parts of sodium metaaluminate and 2 parts of limestone to 40 μm powder for later use, add 15 parts of triisopropanolamine to the reaction kettle, mix and stir the prepared powder at 55°C, and cool to At room temperature, add 5 parts of hydroxymethylmethylcellulose and 5 parts of carboxymethylcellulose, and continue to stir evenly to obtain a composite additive.
[0039] Then, use the above-mentioned product composite additives to prepare mining high-water and high-strength filling materials:
[0040] Weigh A component by mass: 50 parts of sulfoaluminate cement, 5 parts of fly ash, 10 parts of sodium bentonite, 2 parts of tartaric acid, 3 parts of polyacrylamide; B component: 8 parts of dihydrate gypsum, 3 parts of quicklime, 1 part of kaolin, 8 parts of quartz powder, and 10 parts of compound additives.
[0041] The raw materials in the above-mentioned components A and B are mixed in proportion and stirred evenly to obt...
PUM
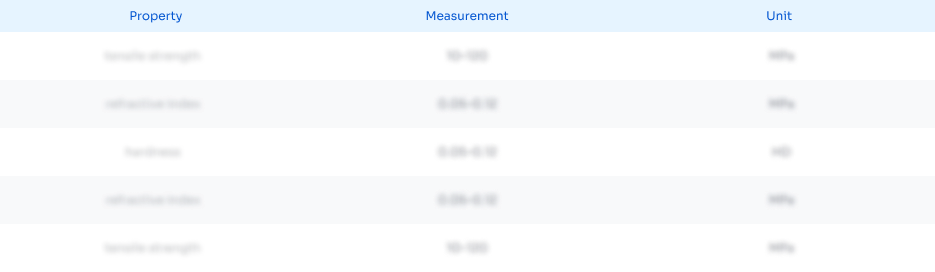
Abstract
Description
Claims
Application Information

- Generate Ideas
- Intellectual Property
- Life Sciences
- Materials
- Tech Scout
- Unparalleled Data Quality
- Higher Quality Content
- 60% Fewer Hallucinations
Browse by: Latest US Patents, China's latest patents, Technical Efficacy Thesaurus, Application Domain, Technology Topic, Popular Technical Reports.
© 2025 PatSnap. All rights reserved.Legal|Privacy policy|Modern Slavery Act Transparency Statement|Sitemap|About US| Contact US: help@patsnap.com