Modeling and optimization design method of variable stiffness composite cylindrical shell
A cylindrical shell and composite material technology, applied in computer-aided design, design optimization/simulation, calculation, etc., can solve problems such as low efficiency, difficult modeling of variable stiffness structures, and long design and analysis cycle, so as to overcome the analysis cycle Excessive length, extensive application and promotion significance, and the effect of improving the efficiency of optimization design
- Summary
- Abstract
- Description
- Claims
- Application Information
AI Technical Summary
Problems solved by technology
Method used
Image
Examples
Embodiment Construction
[0025] This embodiment is a modeling and optimal design method for a variable stiffness composite material cylindrical shell.
[0026] The modeling and optimization design method of the variable stiffness composite cylindrical shell in this embodiment is to carry out element discretization design on the geometric model of the cylindrical shell; then, assign variable stiffness composite material properties to the discrete elements of the geometric model of the cylindrical shell ; Assign variable angle parameters to the discrete units in the model and establish a finite element analysis model; secondly, conduct a small amount of finite element analysis on the parametric analysis model of the discrete units in the model and extract sample points to establish an approximation for buckling analysis and optimal design Model. The modeling and rapid optimization design method realizes the establishment of the simulation analysis model of the variable stiffness composite cylindrical sh...
PUM
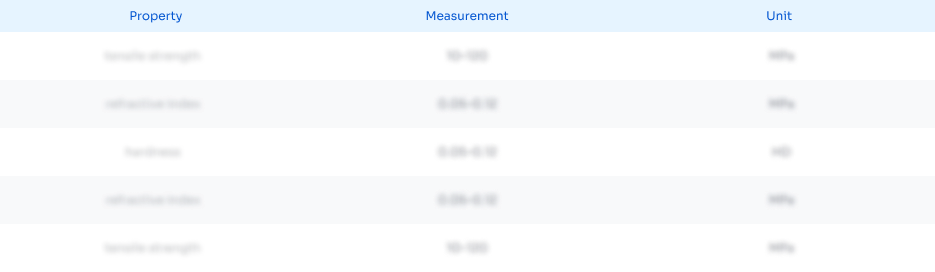
Abstract
Description
Claims
Application Information

- Generate Ideas
- Intellectual Property
- Life Sciences
- Materials
- Tech Scout
- Unparalleled Data Quality
- Higher Quality Content
- 60% Fewer Hallucinations
Browse by: Latest US Patents, China's latest patents, Technical Efficacy Thesaurus, Application Domain, Technology Topic, Popular Technical Reports.
© 2025 PatSnap. All rights reserved.Legal|Privacy policy|Modern Slavery Act Transparency Statement|Sitemap|About US| Contact US: help@patsnap.com