Early-strength dense concrete for shield segment and preparation method of early-strength dense concrete
A technology for compacting concrete and shield segments, which is applied in the field of high-performance concrete, can solve the problems of insufficient concrete slump and expansion, high reinforcement ratio of shield segments, and high price of chemical early-strength agents. effect, increase the difficulty of vibrating, and reduce the effect of steaming time
- Summary
- Abstract
- Description
- Claims
- Application Information
AI Technical Summary
Problems solved by technology
Method used
Image
Examples
Embodiment 1
[0030] (1) Mix and stir fly ash, blast furnace slag powder, and water at a mass ratio of 1:2:17 to prepare slurry A, pump slurry A into a vertical stirring ball mill and grind to obtain a median particle size of 0.3-0.5 μm slurry B;
[0031] (2) Get the spherical fly ash after magnetic separation, the slurry B and the homogenizer in the step (1), mix and stir at a mass ratio of 11:20:0.08, and be mixed with a composite slurry mineral admixture C;
[0032] (3) Take 100 parts of ordinary Portland cement, 60 parts of composite slurry mineral admixture C, 48 parts of water, and 0.5 part of water reducer, and fully stir to obtain concrete cementitious material; then add 220 parts of sand and 340 parts of crushed stone in sequence Parts and 0.5 parts of defoaming agent are fully stirred to obtain an early-strength dense concrete for shield segments.
Embodiment 2
[0034](1) Mix and stir fly ash powder, blast furnace slag powder, and water at a mass ratio of 1:2:17 to prepare slurry A, pump slurry A into a vertical stirring ball mill and grind to obtain a median particle size of 0.3-0.5 μm slurry B;
[0035] (2) Get the spherical fly ash after magnetic separation, the slurry B and the homogenizer in the step (1), mix and stir at a mass ratio of 11:20:0.1, and mix it with a composite slurry mineral admixture C;
[0036] (3) Take 130 parts of ordinary Portland cement, 80 parts of composite slurry mineral admixture C, 63 parts of water, and 1.5 parts of water reducing agent, and fully stir to obtain concrete cementitious material; then add 250 parts of sand and 380 parts of crushed stone in sequence 1 part of antifoaming agent and 1 part of defoaming agent are fully stirred to obtain an early-strength compact concrete for shield segment.
Embodiment 3
[0038] (1) Mix and stir fly ash powder, blast furnace slag powder, and water at a mass ratio of 1:2:17 to prepare slurry A, pump slurry A into a vertical stirring ball mill and grind to obtain a median particle size of 0.3-0.5 μm slurry B;
[0039] (2) Get the spherical fly ash after magnetic separation, slurry B and leveling agent in step (1), mix and stir by mass ratio 11:20:0.14, be mixed with composite slurry mineral admixture C;
[0040] (3) Take 120 parts of ordinary Portland cement, 65 parts of composite slurry mineral admixture C, 55 parts of water, and 0.8 parts of water reducer, and stir fully to obtain concrete cementitious material; then add 230 parts of sand and 350 parts of crushed stone in sequence Parts and 0.7 parts of defoaming agent are fully stirred to obtain an early-strength dense concrete for shield segments.
PUM
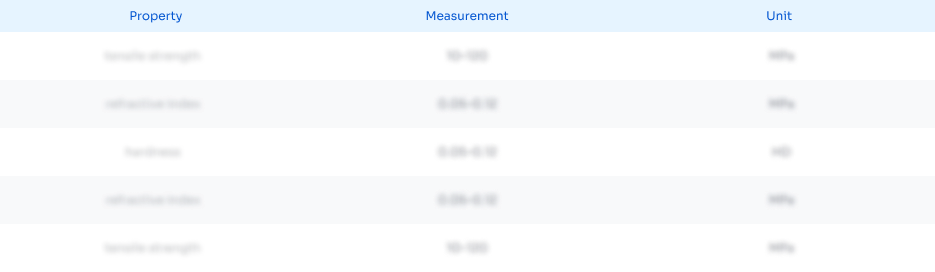
Abstract
Description
Claims
Application Information

- Generate Ideas
- Intellectual Property
- Life Sciences
- Materials
- Tech Scout
- Unparalleled Data Quality
- Higher Quality Content
- 60% Fewer Hallucinations
Browse by: Latest US Patents, China's latest patents, Technical Efficacy Thesaurus, Application Domain, Technology Topic, Popular Technical Reports.
© 2025 PatSnap. All rights reserved.Legal|Privacy policy|Modern Slavery Act Transparency Statement|Sitemap|About US| Contact US: help@patsnap.com