Antistatic agent and preparation method thereof
A technology of antistatic agent and mass fraction, applied in the field of antistatic agent and its preparation, can solve the problems of insufficiently dense structure and decreased antistatic ability, and achieve the effects of reducing impurities, improving binding ability and high product purity
- Summary
- Abstract
- Description
- Claims
- Application Information
AI Technical Summary
Problems solved by technology
Method used
Image
Examples
preparation example 1
[0044] Preparation example 1: the preparation of boric acid monoglyceride adopts the following steps:
[0045] S1: Weigh 20kg of glycerin, add it into the reaction kettle, heat and stir at 60°C;
[0046] S2: Using nitrogen as a protective gas, add 10kg of borax to glycerin. After the borax and glycerin are mixed evenly, adjust the temperature of the reactor to 100°C and carry out condensation and reflux until no more condensed water flows out, and then vacuumize for 1 hour. , to get crude products;
[0047] S3: Filtrate the crude product while it is hot, and then conduct fractional distillation to obtain boric acid monoglyceride.
preparation example 2
[0048] Preparation example 2: the preparation of ethoxylated boric acid monoglyceride (being a kind of in boric acid ester), adopts the following steps:
[0049] S1: Add 10 kg of boric acid monoglyceride and 20 kg of ethyl acetate obtained in Preparation Example 1 to the reactor, and add 0.5 kg of boron trifluoride as a catalyst, and heat the solution to 130° C. in the reactor;
[0050] S2: With nitrogen as the protective gas, 5 kg of ethylene oxide was passed into the boric acid monoglyceride solution, and the reaction time was 3 hours;
[0051] S3: filter the reacted mixed solution and then distill to obtain ethoxylated boric acid monoglyceride.
preparation example 3
[0052] Preparation example 3: the preparation of boric acid monoglyceride octadecanoate (being a kind of in boric acid ester), adopts the following steps:
[0053] S1: Add 10kg boric acid monoglyceride and sufficient dimethyl fumarate obtained in Preparation Example 1 in the reactor, and add 0.8kgDMF (dimethylformamide) as a catalyst;
[0054] S2: Add 20kg of stearic acid to the reaction kettle, and heat the solution to 120°C. During the heating process, carry out condensing and reflux to continuously discharge the condensed water, and the reaction time is 4 hours;
[0055] S3: filter the reacted mixed solution and then distill to obtain boric acid monoglyceride octadecanoate.
PUM
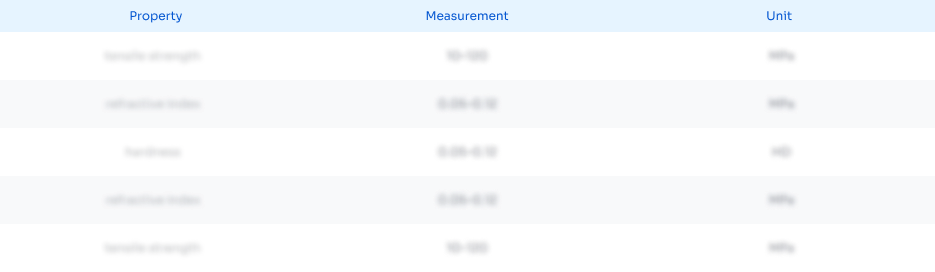
Abstract
Description
Claims
Application Information

- R&D Engineer
- R&D Manager
- IP Professional
- Industry Leading Data Capabilities
- Powerful AI technology
- Patent DNA Extraction
Browse by: Latest US Patents, China's latest patents, Technical Efficacy Thesaurus, Application Domain, Technology Topic, Popular Technical Reports.
© 2024 PatSnap. All rights reserved.Legal|Privacy policy|Modern Slavery Act Transparency Statement|Sitemap|About US| Contact US: help@patsnap.com