Hydraulic actuator for robot
A hydraulic actuation and robot technology, applied in fluid pressure actuation devices, fluid pressure actuation system testing, mechanical equipment, etc., can solve the problem of inability to achieve impact buffering, impact energy absorption, and controllable release of impact energy stored problems, to achieve the effect of increasing anti-interference ability, reducing energy consumption, and high load capacity
- Summary
- Abstract
- Description
- Claims
- Application Information
AI Technical Summary
Problems solved by technology
Method used
Image
Examples
Embodiment 1
[0038]Such asFigure 1-14 As shown, a hydraulic actuator mechanism for a robot includes a vane-type swing hydraulic motor, a rotary encoder, a servo valve, a high-speed three-position four-way electromagnetic directional valve, a pressure reducing valve, a one-way valve, an accumulator, and two A pressure sensor, a rotary encoder is installed at the tail of a vane-type swing hydraulic motor. The vane swing hydraulic motor is cylindrical and includes an output shaft, a head carbon fiber end cover 6, a tail carbon fiber end cover 23, and two bearing end covers 5. Two sets of needle bearings 46, head aluminum alloy gland 30, tail aluminum alloy gland 24, main aluminum alloy cylinder 29, auxiliary aluminum alloy cylinder 25, middle partition 27, outer end of head aluminum alloy gland 30 Connected with the first bearing end cover, the head aluminum alloy gland 30 is equipped with the first needle roller bearing, the head aluminum alloy gland 30 is connected to the outer carbon fiber end c...
PUM
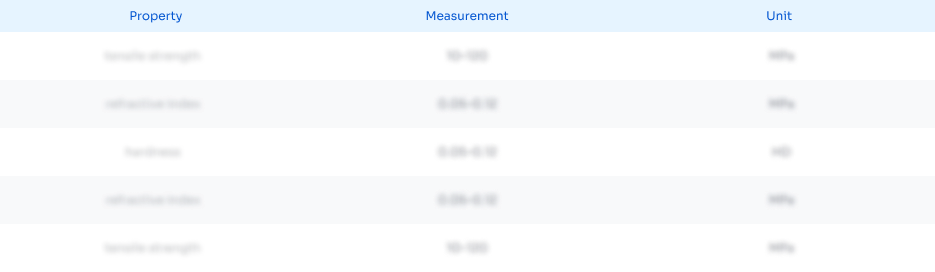
Abstract
Description
Claims
Application Information

- Generate Ideas
- Intellectual Property
- Life Sciences
- Materials
- Tech Scout
- Unparalleled Data Quality
- Higher Quality Content
- 60% Fewer Hallucinations
Browse by: Latest US Patents, China's latest patents, Technical Efficacy Thesaurus, Application Domain, Technology Topic, Popular Technical Reports.
© 2025 PatSnap. All rights reserved.Legal|Privacy policy|Modern Slavery Act Transparency Statement|Sitemap|About US| Contact US: help@patsnap.com