Method for predicting compression rigidity and compression strength of composite material spiral structure by considering geometric nonlinearity
A geometrically nonlinear, composite technology, applied in the field of predicting the compressive stiffness and compressive strength of composite helical structures, which can solve the problems of complex calculation, high cost of compressive stiffness and compressive strength, and difficult to guarantee calculation accuracy.
- Summary
- Abstract
- Description
- Claims
- Application Information
AI Technical Summary
Problems solved by technology
Method used
Image
Examples
Embodiment Construction
[0108] Step 1, defining the geometric shape and size of the helical structure of the composite material, and determining the mathematical expression of the relationship between various geometric parameters.
[0109] The overall appearance of the helical helix structure of the composite material is helical, and the cross section is circular. The composite material used can be a unidirectional reinforced composite material or a plane braided composite material. The helical structure of the composite material has elastic deformation ability along the direction of the helical axis. A compressive load is applied along the helical axis at both ends of the helical helical antenna of the composite material, and the pitch decreases. After the compressive load is removed, the helical structure of the composite material recovers to initial configuration.
[0110] In order to establish a theoretical prediction model for the compression performance of the composite helical structure, the fol...
PUM
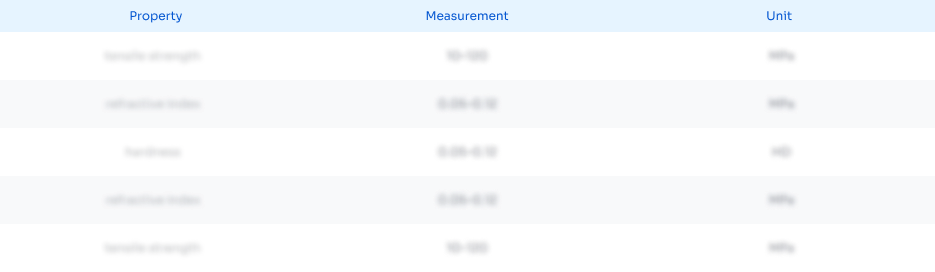
Abstract
Description
Claims
Application Information

- R&D
- Intellectual Property
- Life Sciences
- Materials
- Tech Scout
- Unparalleled Data Quality
- Higher Quality Content
- 60% Fewer Hallucinations
Browse by: Latest US Patents, China's latest patents, Technical Efficacy Thesaurus, Application Domain, Technology Topic, Popular Technical Reports.
© 2025 PatSnap. All rights reserved.Legal|Privacy policy|Modern Slavery Act Transparency Statement|Sitemap|About US| Contact US: help@patsnap.com