Organic lithium soap composite urea-based lubricating grease and preparation method thereof
A compound urea-based grease and organic lithium technology, which is applied in lubricating compositions, petroleum industry, thickeners, etc., can solve the problems of grease hardening and oxidation stability degradation, complicated preparation operations, and restrictions on popularization and application. The effect of improving mechanical stability
- Summary
- Abstract
- Description
- Claims
- Application Information
AI Technical Summary
Problems solved by technology
Method used
Image
Examples
Embodiment 1
[0044] Take 300g of mineral oil with a viscosity of 20sCt at 100°C and put it into the reaction kettle, add 13.1g of octadecylamine, 13g of oleylamine, 4.8g of cyclohexylamine, 26.1g of N-aminoethylpiperazine, stir and heat, and keep the temperature at 80 ℃. At the same time, add 300g of base oil and 48.8g of 4,4`-diphenylmethane diisocyanate into another reaction kettle, heat to dissolve, keep the temperature constant at 80°C, and mix the two solutions through a dynamic material mixer within 5 to 8 minutes. Reaction, after entering the intermediate tank, control the temperature at 95°C, and react for 60 minutes. Then add 22g of 12-hydroxystearic acid, 5.2g of azelaic acid, and 2.1g of boric acid successively, stir evenly, add 54g of 10% lithium hydroxide solution, stir and heat, raise the temperature to 160°C, keep the temperature for 1 hour, and then heat to Refining temperature (160-180°C), add 100g surplus quenching oil, when the temperature drops below 80°C, take out the...
Embodiment 2
[0046] Take 300g of mineral oil with a viscosity of 20sCt at 100°C and put it into a fat-making kettle, add 8.1g of octadecylamine, 6g of cyclohexylamine, and 19.1g of N-aminoethylpiperazine, stir and heat, and keep the temperature at 85°C. Add 260g of base oil and 38.2g of 4,4`-diphenylmethane diisocyanate into another reaction kettle, heat to dissolve, keep the temperature at 80°C, and react the two solutions through a dynamic material mixer within 2 to 4 minutes , after entering the intermediate kettle, control the temperature at 90°C, and react for 60 minutes. Then, add 26g of 12-hydroxystearic acid, 5.7g of azelaic acid, after stirring evenly, slowly add 49g of 10% lithium hydroxide solution and stir and heat, heat up to 160°C, keep the temperature for 1 hour, after that, heat to the refining temperature ( 160-180°C), add 100g of surplus quenching oil, when the temperature drops below 80°C, take out the kettle and grind three times with a three-roll machine. The product p...
Embodiment 3
[0048]Take 300g of PAO20 synthetic oil with a viscosity of 20sCt at 100°C and add it to the fat-making kettle, and add 13.6g of octadecylamine, 13.5g of oleylamine, 2.5g of cyclohexylamine, and 15.4g of N-aminoethylpiperazine, stir and heat, and the temperature Keep the temperature constant at 65°C, add 165g of base oil and 38.2g of 4,4`-diphenylmethane diisocyanate into another reactor at the same time, heat to dissolve, keep the temperature constant at 80°C, pass the two solutions within 2 to 4 minutes The reaction was carried out in a dynamic material mixer, and after entering the intermediate tank, the temperature was controlled at 87°C and the reaction was carried out for 60 minutes. Then, add 18g of 12-hydroxystearic acid, 3.2g of boric acid, slowly add 42g of 15% lithium hydroxide solution, stir and heat, raise the temperature to 160°C, keep the temperature for 1 hour, after that, heat to the refining temperature (160-180°C ), add 100g surplus quenching oil, when the te...
PUM
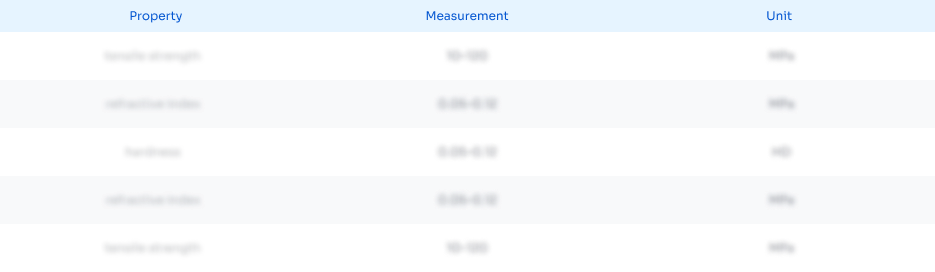
Abstract
Description
Claims
Application Information

- Generate Ideas
- Intellectual Property
- Life Sciences
- Materials
- Tech Scout
- Unparalleled Data Quality
- Higher Quality Content
- 60% Fewer Hallucinations
Browse by: Latest US Patents, China's latest patents, Technical Efficacy Thesaurus, Application Domain, Technology Topic, Popular Technical Reports.
© 2025 PatSnap. All rights reserved.Legal|Privacy policy|Modern Slavery Act Transparency Statement|Sitemap|About US| Contact US: help@patsnap.com