Production process for solving pitted surfaces of low-carbon steel wires
A production process and low-carbon steel technology, applied in the field of metallurgy, can solve the problems that cannot meet the customer's 0.5mm light drawing process requirements, pockmarks, and cannot be rolled and reduced, so as to increase the function of backflushing water and reduce the amount of steel passing Effect
- Summary
- Abstract
- Description
- Claims
- Application Information
AI Technical Summary
Problems solved by technology
Method used
Image
Examples
Embodiment 1
[0029] A production process for solving pitting on the surface of low-carbon steel wire rods, the main process parameters are:
[0030] (1) The temperature in the heating furnace is set as follows: heating section 800°C, heating section 2 990°C, soaking section 1070°C;
[0031] (2) Set the air-fuel ratio to 0.50-0.65;
[0032] (3) The high-pressure water dephosphorization setting water pressure is ≥12MPa;
[0033] (4) The temperature of each key point of the rolling line is: the rolling start temperature is 1000°C, the cutting and sizing temperature is 865°C, and the spinning temperature is 865°C;
[0034] (5) Increase the back blowing water function of the water tank;
[0035] (6) Control the amount of steel passed, and achieve the purpose of actually reducing the amount of steel passed by increasing the regulation of the amount of steel passed in intermediate rolling. The actual rolling tonnage of the rolling groove before rolling must be less than the set tonnage, as sho...
Embodiment 2
[0039] (1) The temperature in the heating furnace is set as follows: the heating stage 1 is 850°C, the heating stage 2 is 1050°C, and the soaking stage is 1100°C;
[0040] (2) Set the air-fuel ratio to 0.50-0.65;
[0041] (3) The high-pressure water dephosphorization setting water pressure is ≥12MPa;
[0042] (4) The temperature of each key point of the rolling line is: the rolling start temperature is 1030°C, the cutting and sizing temperature is 875°C, and the spinning temperature is 885°C;
[0043] (5) Increase the back blowing water function of the water tank;
[0044] (6) Control the amount of steel passed, and achieve the purpose of actually reducing the amount of steel passed by increasing the regulation of the amount of steel passed in intermediate rolling. The actual rolling tonnage of the rolling groove before rolling must be less than the set tonnage, as shown in Table 1.
[0045] In "Q320582 JYG20-2019 Cold Heading Steel Hot-Rolled Wire Rod for Light Drawing (Re...
Embodiment 3
[0048] (1) The temperature in the heating furnace is set as follows: heating section 1 is 900°C, heating section 2 is 1090°C, and soaking section is 1150°C;
[0049] (2) Set the air-fuel ratio to 0.50-0.65;
[0050] (3) The high-pressure water dephosphorization setting water pressure is ≥12MPa;
[0051] (4) The temperature of each key point of the rolling line is: the rolling start temperature is 1060°C, the cutting and sizing temperature is 895°C, and the spinning temperature is 905°C;
[0052] (5) Increase the back blowing water function of the water tank;
[0053] (6) Control the amount of steel passed, and achieve the purpose of actually reducing the amount of steel passed by increasing the regulation of the amount of steel passed in intermediate rolling. The actual rolling tonnage of the rolling groove before rolling must be less than the set tonnage, as shown in Table 1.
[0054] In "Q320582 JYG20-2019 Cold Heading Steel Hot-Rolled Wire Rod for Light Drawing (Review D...
PUM
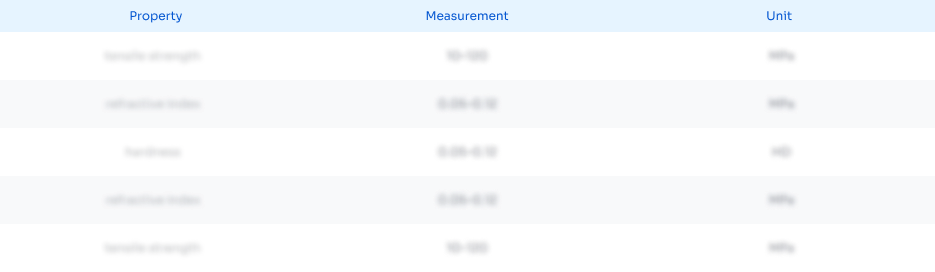
Abstract
Description
Claims
Application Information

- R&D
- Intellectual Property
- Life Sciences
- Materials
- Tech Scout
- Unparalleled Data Quality
- Higher Quality Content
- 60% Fewer Hallucinations
Browse by: Latest US Patents, China's latest patents, Technical Efficacy Thesaurus, Application Domain, Technology Topic, Popular Technical Reports.
© 2025 PatSnap. All rights reserved.Legal|Privacy policy|Modern Slavery Act Transparency Statement|Sitemap|About US| Contact US: help@patsnap.com