Etching liquid for copper foils, method for producing printed wiring board using said etching liquid, etching liquid for electrolytic copper layers, and method for producing copper pillar with electrolytic copper layers
A technology of etching solution and electrolytic copper, which is applied in the manufacture of printed circuits, removal of conductive materials by chemical/electrolytic methods, printed circuits, etc.
- Summary
- Abstract
- Description
- Claims
- Application Information
AI Technical Summary
Problems solved by technology
Method used
Image
Examples
preparation example Construction
[0075] [Preparation of etching solution]
[0076] The etching solution of the present invention can be prepared by uniformly stirring (A) component, (B) component, (C) component, and other components as needed. The stirring method of these components is not particularly limited, and the stirring method generally used in the preparation of etching solution can be adopted.
[0077] [Use of etching solution]
[0078] The etching liquid of this invention can be used suitably for etching of copper foil. For example, the etchant of the present invention can be suitably used for etching copper foil in an ETS process. In addition, the etchant of the present invention can be used for other uses requiring etching of copper foil in addition to etching of copper foil in the ETS process.
[0079] According to a preferred aspect of the present invention, by performing etching using the etching solution of the present invention, the etching rate and wiring shape become more favorable. In...
Embodiment 1
[0150] Into a glass beaker with a capacity of 1 L, 0.949 kg of pure water, 0.033 kg of hydrogen peroxide (A) (manufactured by Mitsubishi Gas Chemical Co., Ltd., 60% by mass, molecular weight 34) and sulfuric acid (B) (manufactured by Mitsubishi Gas Chemical Co., Ltd.) were charged. , 46% by mass of dilute sulfuric acid, 0.017 kg of molecular weight (98), and 0.0003 kg of 5-amino-1H-tetrazole (manufactured by Masuda Chemical Industry Co., Ltd.) as the azole compound (C). Stirring is performed to form a uniform state, and an etching solution is prepared.
[0151] Using this etchant, the substrate for evaluation was subjected to a spray process of etching to a thickness of 8 μm of copper foil at a liquid temperature of 30° C. and a spray pressure of 0.15 MPa.
[0152] In order to determine the etching treatment time for copper foil with a thickness of 8 μm, the entire copper foil substrate (size 40mm×40mm) was sprayed for 60 seconds at a liquid temperature of 30°C, and the amount...
Embodiment 2
[0157] An etching solution was prepared in the same manner as in Example 1 except that phenylurea was used in the quantitative ratio described in Table 1, and after spraying the substrate for evaluation, the amount of side etching was evaluated.
PUM
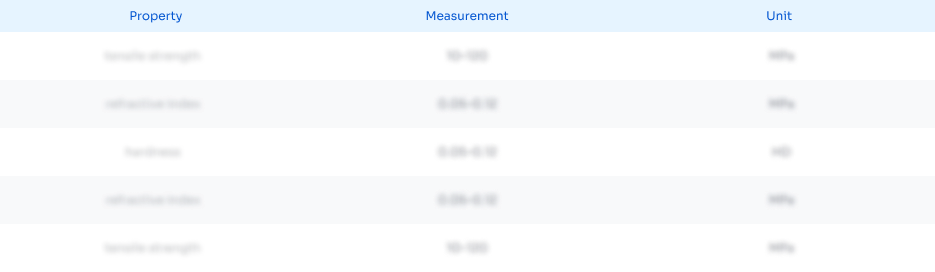
Abstract
Description
Claims
Application Information

- R&D Engineer
- R&D Manager
- IP Professional
- Industry Leading Data Capabilities
- Powerful AI technology
- Patent DNA Extraction
Browse by: Latest US Patents, China's latest patents, Technical Efficacy Thesaurus, Application Domain, Technology Topic, Popular Technical Reports.
© 2024 PatSnap. All rights reserved.Legal|Privacy policy|Modern Slavery Act Transparency Statement|Sitemap|About US| Contact US: help@patsnap.com