A phase-to-phase coupled axial flux reluctance motor without stator yoke
A technology of axial flux and reluctance motors, applied in the direction of magnetic circuits, electromechanical devices, electrical components, etc., can solve the large torque ripple and eddy current loss of the motor, increase the iron loss and eddy current loss of the motor, and reduce the dynamic response of the motor Speed and other issues to achieve the effect of reducing motor loss, increasing power density, and increasing the range of output torque
- Summary
- Abstract
- Description
- Claims
- Application Information
AI Technical Summary
Problems solved by technology
Method used
Image
Examples
Embodiment Construction
[0031] The phase-to-phase coupling axial flux reluctance motor without stator yoke is a multi-phase motor. The number of stator poles of the motor is even, the number of motor phases is M, and the number of motor stator poles is N. The relationship between the number of motor phases and the number of motor stator poles It is: N=K×M, K=2,3,4,5,6…where the number of motor phases M≥5 and is an odd number, and the number of rotor poles H=K×(M+1) / 2.
[0032] The present invention introduces an axial flux reluctance motor with a 7-phase stator-rotor pole number ratio of 14 / 8 without a stator yoke and an axial flux reluctance motor. block structure.
[0033] like figure 1 As shown, the stator structure of the motor is composed of iron core 2 and coil winding 3. The coil windings are respectively wound on the corresponding stator core. When winding on the stator core, the winding method is not fixed but the direction is the same. For specific grouping methods, see figure 1, the sta...
PUM
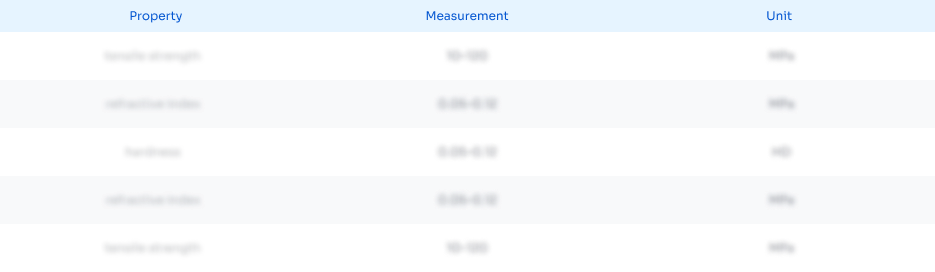
Abstract
Description
Claims
Application Information

- R&D
- Intellectual Property
- Life Sciences
- Materials
- Tech Scout
- Unparalleled Data Quality
- Higher Quality Content
- 60% Fewer Hallucinations
Browse by: Latest US Patents, China's latest patents, Technical Efficacy Thesaurus, Application Domain, Technology Topic, Popular Technical Reports.
© 2025 PatSnap. All rights reserved.Legal|Privacy policy|Modern Slavery Act Transparency Statement|Sitemap|About US| Contact US: help@patsnap.com