Engine box body positioning structure
A positioning structure and engine technology, applied in the direction of the injection device, etc., can solve the problems of damage to the casing, paint sprayed into the chamber of the box, easy to move, etc., and achieve the effect of improving stability
- Summary
- Abstract
- Description
- Claims
- Application Information
AI Technical Summary
Problems solved by technology
Method used
Image
Examples
Embodiment 1
[0061] Such as Figure 1 to Figure 11 As shown, the positioning structure of the engine case includes a support base 1 and a shielding plate 21, and a positioning seat 2 is connected to the support base 1;
[0062] The positioning seat 2 is movable up and down and is connected with a locking rod 19 which can rotate circumferentially. The top of the locking rod 19 runs through the top of the positioning seat 2, and the top of the locking rod 19 is also connected with a Circular locking block 20;
[0063] The positioning seat 2 is also provided with a locking rod elastic part 22, and the locking rod elastic part 22 acts on the locking rod 19, so that the locking rod 19 is located at the extreme position of downward movement, and the locking block 20 is located at the movable plate 3 above;
[0064] The side end of the shielding plate 21 also has a shielding extension 23, and the bottom end of the shielding plate 21 is provided with a locking groove 24 that can cooperate with t...
Embodiment 2
[0070] This embodiment makes the following further limitations on the basis of Embodiment 1: the positioning seat 2 is provided with a positioning seat annular groove 25, and the locking rod 19 is sleeved and connected with a ring that can rotate in the positioning seat annular groove 25 And the locking rod moving up and down abuts against the ring 26;
[0071] The locking rod elastic member 22 is sheathed on the locking rod 19 , and the upper and lower ends of the locking rod elastic member 22 abut against the top of the annular groove 25 of the positioning seat and the top of the locking rod abutting ring 26 respectively.
[0072] In this embodiment, through the cooperation between the locking rod abutment ring 26 and the annular groove 25 of the positioning seat, not only can the relative rotation between the locking rod 19 and the positioning seat 2 be realized, but also be used to limit the locking rod 19 up and down. The extreme position of movement avoids excessive move...
Embodiment 3
[0074] This embodiment makes the following further limitations on the basis of Embodiment 1: the locking rod 19 is provided with a circumferential locking groove 27 and a circumferential limiter located below the circumferential locking groove 27 and communicating with the circumferential locking groove 27. Position groove 28, the opening arc length of the circumferential limiting groove 28 along the circumferential direction of the locking rod 19 is greater than the opening arc length of the circumferential locking groove 27 along the circumferential direction of the locking rod 19;
[0075] The positioning seat 2 is also provided with a circumferential locking protrusion 29 which can fit into the circumferential locking groove 27 , and the circumferential locking protrusion 29 can be located in the circumferential limiting groove 28 .
[0076] In this embodiment, the bottom end of the circumferential locking groove 27 communicates with the top end of one end of the circumfere...
PUM
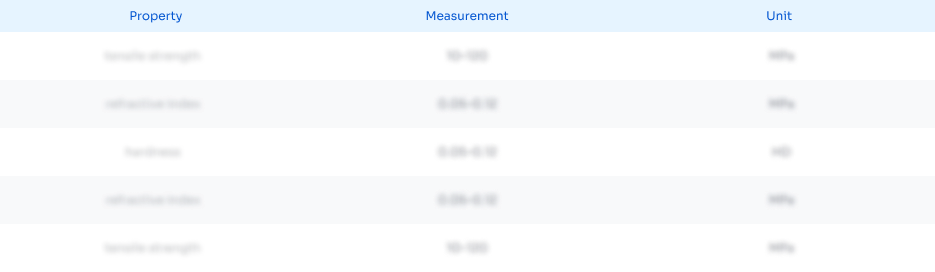
Abstract
Description
Claims
Application Information

- Generate Ideas
- Intellectual Property
- Life Sciences
- Materials
- Tech Scout
- Unparalleled Data Quality
- Higher Quality Content
- 60% Fewer Hallucinations
Browse by: Latest US Patents, China's latest patents, Technical Efficacy Thesaurus, Application Domain, Technology Topic, Popular Technical Reports.
© 2025 PatSnap. All rights reserved.Legal|Privacy policy|Modern Slavery Act Transparency Statement|Sitemap|About US| Contact US: help@patsnap.com