Longitudinal hole forming method for layered thermal barrier coating based on reverse deformation, and thermal barrier coating
A thermal barrier coating and reverse deformation technology, applied in coatings, metal material coating processes, melt spraying, etc., can solve the problem of weakening thermal insulation of coatings, increasing pore-forming stress, and unavoidable coating sintering and densification. and other problems, to achieve the effect of improving service life, prolonging service life, and quickly realizing engineering applications.
- Summary
- Abstract
- Description
- Claims
- Application Information
AI Technical Summary
Problems solved by technology
Method used
Image
Examples
Embodiment 1
[0049] A low-temperature longitudinal hole-forming method of a high-insulation layered thermal barrier coating based on reverse deformation, comprising the following steps:
[0050] In step 1, a disc-shaped nickel-based superalloy is selected as the metal substrate 1. The disc-shaped nickel-based superalloy has a diameter of 25.4 mm and a thickness of 3 mm, and its model is Inconel738. A metal bonding layer 2 with a thickness of 80 μm is prepared on the upper surface of the metal substrate 1 by a plasma spraying process. The material of the metal bonding layer 2 is spherical NiCoCrAlTaY powder with a particle size of 10 μm-50 μm. The spraying power is 35kW, the main gas argon is 40L / min, the auxiliary gas hydrogen is 7L / min, the spraying distance is 120mm, and the speed of the gun is 600mm / s.
[0051] Step 2, preparing a 500 μm ceramic heat insulating layer 3 on the metal bonding layer 2 by using a plasma spraying process. The powder of the ceramic coating is yttria-stabiliz...
Embodiment 2
[0057] The difference between this example and example 1 is that in step 3.2, the water flow pressure used is 21 MPa, the resulting longitudinal pore depth is 30% to 60% of the coating thickness, and the pore interval is 0.6 to 4 times the coating thickness. times.
Embodiment 3
[0059] The difference between this embodiment and embodiment 1 is that in step 1, a metal bonding layer 2 with a thickness of 50 μm is deposited on the metal substrate 1, and in step 2, a ceramic with a thickness of 200 μm is deposited on the metal bonding layer 2. Insulation layer3. In step 3, heat the thermal barrier coating and the metal substrate 1 simultaneously to 200°C within 3 minutes, and then continue to heat the metal substrate 1 to 600°C, and at the same time impact with a water flow with a velocity of 50m / s and a pressure of 5MPa. The ceramic heat insulation layer 3 is used to make the temperature difference between the ceramic heat insulation layer 3 and the metal base 1 be 550° C. after heating.
PUM
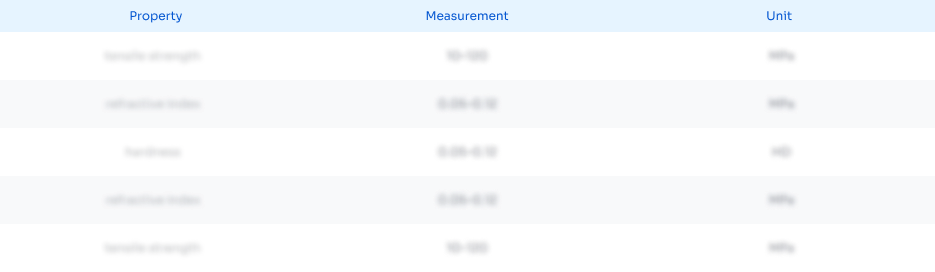
Abstract
Description
Claims
Application Information

- R&D Engineer
- R&D Manager
- IP Professional
- Industry Leading Data Capabilities
- Powerful AI technology
- Patent DNA Extraction
Browse by: Latest US Patents, China's latest patents, Technical Efficacy Thesaurus, Application Domain, Technology Topic, Popular Technical Reports.
© 2024 PatSnap. All rights reserved.Legal|Privacy policy|Modern Slavery Act Transparency Statement|Sitemap|About US| Contact US: help@patsnap.com