Three-dimensional pattern coating and preparation method thereof, lamp accessory and lamp
A three-dimensional pattern and coating technology, which is applied to coatings, lighting and heating equipment, and parts of lighting devices, can solve the problems of multiple processes, large color difference range, and high cost, and achieve simple process, unique pattern, and wide application range wide effect
- Summary
- Abstract
- Description
- Claims
- Application Information
AI Technical Summary
Problems solved by technology
Method used
Image
Examples
preparation example Construction
[0043] figure 1 A schematic flow chart showing a method for preparing a three-dimensional pattern coating according to an embodiment of the present invention is shown. see figure 1 As shown, the preparation method may at least include the following steps S10 to S50.
[0044] Step S10: Perform pretreatment on the substrate.
[0045] The substrate can be a metal substrate, such as aluminum, copper, iron, etc., which is selected according to actual application requirements, and the present invention does not specifically limit it. The shape of the substrate can also be selected according to actual application requirements, for example, a ring shape, a flat plate shape, and the like. By pre-treating the substrate, the cleaning and / or protection of the substrate can be achieved, so as to prepare for the subsequent application of coatings.
[0046] Step S20: coating a first thickness of thermosetting acrylic resin-based primer on the substrate, the first thickness being in the r...
Embodiment 1
[0075] An iron substrate is used in this embodiment.
[0076] Step 1: Sanding. 180-mesh sandpaper and 600-mesh sandpaper were used for rough polishing and fine polishing of the iron substrate, respectively.
[0077] Step 2: Degrease. Degrease the iron substrate by immersing it in a general degreasing agent at 40°C for 20 minutes. The ingredients of the universal degreaser are as described above.
[0078] Step 3: Wash with water. Wash with pH7-8 water for 2 minutes at room temperature to remove residual degreasing agent.
[0079] Step 4: Rust removal. Use a rust remover with a full acidity of 6-10pt at room temperature for 15 minutes to remove the rust on the surface of the iron substrate. The ingredients of the rust remover are as mentioned above.
[0080] Step 5: Wash with water. Specifically, first wash with pH 5-6 water at room temperature for 2 minutes, and then wash with pH 6-7 water for 2 minutes at room temperature to remove residual rust remover.
[0081] Step...
Embodiment 2
[0096] The difference between this embodiment and Embodiment 1 is only:
[0097] The spraying thickness of the primer is 11 μm, and titanium dioxide is used as a colored filler in the primer. The spraying thickness of the topcoat is 11 μm, and the cracking agent in the topcoat is 9006-65-8 type cracking agent with a content of 0.5wt%. Finally, a three-dimensional pattern coating with white background color and uniform cracks is obtained. The three-dimensional pattern coating prepared in this embodiment has passed the 100-grid test, the paint film hardness test, the salt spray test, the alternating damp heat test and the cold and heat shock resistance test, and its adhesion, hardness, corrosion resistance, alternating resistance and resistance Both cold and heat shock properties are qualified.
PUM
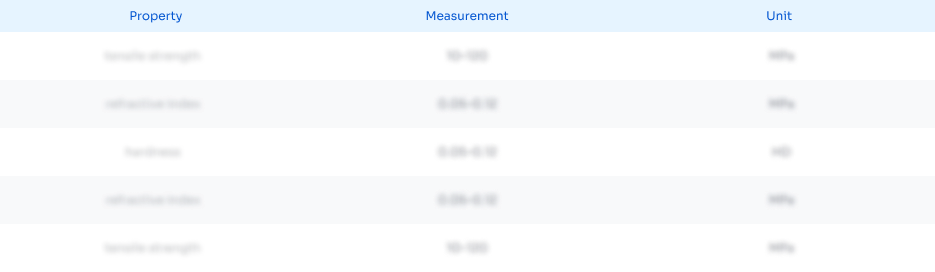
Abstract
Description
Claims
Application Information

- R&D
- Intellectual Property
- Life Sciences
- Materials
- Tech Scout
- Unparalleled Data Quality
- Higher Quality Content
- 60% Fewer Hallucinations
Browse by: Latest US Patents, China's latest patents, Technical Efficacy Thesaurus, Application Domain, Technology Topic, Popular Technical Reports.
© 2025 PatSnap. All rights reserved.Legal|Privacy policy|Modern Slavery Act Transparency Statement|Sitemap|About US| Contact US: help@patsnap.com