Torque ripple suppression method for direct-drive wind turbine generator
A wind turbine, torque ripple technology, applied in motor control, motor generator control, AC motor control, etc., can solve problems such as inverter nonlinearity, large electromagnetic torque ripple, and large harmonics in stator current. To achieve the effect of stable operation process and strong practicability
- Summary
- Abstract
- Description
- Claims
- Application Information
AI Technical Summary
Problems solved by technology
Method used
Image
Examples
Embodiment Construction
[0060] The specific implementation manners of the present invention will be further described in detail below in conjunction with the accompanying drawings and embodiments. The following examples are used to illustrate the present invention, but are not intended to limit the scope of the present invention.
[0061] A direct-drive wind turbine torque ripple suppression method, such as figure 1 shown, including the following steps:
[0062] Step 1: by performing dq rotation coordinate transformation on the voltage and current of the permanent magnet synchronous generator (PMSG);
[0063] The mathematical relationship equations of the voltage and current of PMSG in the dq synchronous rotating coordinate system are:
[0064]
[0065] Among them, i d and i q Respectively d-axis and q-axis current; u d and u q Respectively d-axis and q-axis voltage; R s is the stator resistance; ω is the electrical angular frequency of the generator; L d and L q are d-axis and q-axis ind...
PUM
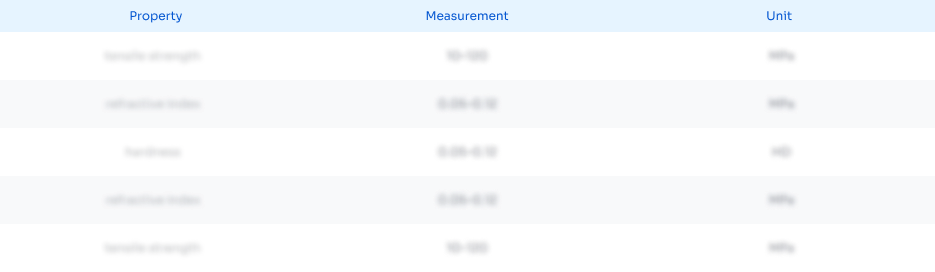
Abstract
Description
Claims
Application Information

- R&D Engineer
- R&D Manager
- IP Professional
- Industry Leading Data Capabilities
- Powerful AI technology
- Patent DNA Extraction
Browse by: Latest US Patents, China's latest patents, Technical Efficacy Thesaurus, Application Domain, Technology Topic, Popular Technical Reports.
© 2024 PatSnap. All rights reserved.Legal|Privacy policy|Modern Slavery Act Transparency Statement|Sitemap|About US| Contact US: help@patsnap.com