Motor torque zero-crossing anti-shake control method for new energy vehicles
A new energy vehicle, motor torque technology, applied in the direction of control drive, control device, vehicle components, etc., can solve the torque response speed and response accuracy deterioration, new energy vehicles have a large impact on power, reduce speed fluctuations and torque shocks, etc. problems, to achieve the effect of smooth torque changes, improve driving experience, reduce speed fluctuations and power shocks
- Summary
- Abstract
- Description
- Claims
- Application Information
AI Technical Summary
Problems solved by technology
Method used
Image
Examples
specific Embodiment
[0049]Step 1: The torque request command from the ride controller unit VCU or the torque request command from other control terminals is sent to the motor controller PEU, combined with the existing torque zero-crossing identification algorithm to determine whether it is a torque zero-crossing condition, and if so, execute Step 2, otherwise, the output torque is equal to the requested torque, and continue to be kept in step 1, and the zero-crossing condition is monitored in real time;
[0050] Step 2: Confirm that it belongs to the torque zero-crossing condition. Use a torque slope of 100Nm / s to limit the response speed of the output torque following the torque command within 0.1 seconds of the set time. The limited output torque cannot exceed the requested torque, and then perform step 3;
[0051] Step 3: Determine whether the requested torque command has a torque zero-crossing condition again within the time limit of the torque output slope, if yes, return to step 1; otherwise...
PUM
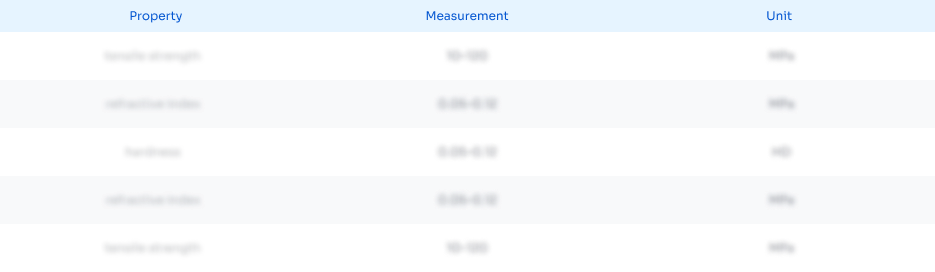
Abstract
Description
Claims
Application Information

- R&D
- Intellectual Property
- Life Sciences
- Materials
- Tech Scout
- Unparalleled Data Quality
- Higher Quality Content
- 60% Fewer Hallucinations
Browse by: Latest US Patents, China's latest patents, Technical Efficacy Thesaurus, Application Domain, Technology Topic, Popular Technical Reports.
© 2025 PatSnap. All rights reserved.Legal|Privacy policy|Modern Slavery Act Transparency Statement|Sitemap|About US| Contact US: help@patsnap.com