Veneer processing technology and processing device used for density fiberboard
A veneer treatment and density board technology, which is applied in wood treatment, wood treatment details, veneer presses, etc., can solve the problem of insufficient lamination between density board and veneer material, and inconvenience of density board and veneer material limit , bubbling, delamination, no peeling, cracking and other problems, to achieve the effect of improving the decoration quality, easy disassembly, easy replacement or maintenance
- Summary
- Abstract
- Description
- Claims
- Application Information
AI Technical Summary
Problems solved by technology
Method used
Image
Examples
Embodiment 1
[0032] A veneer treatment process for density boards, comprising the following steps:
[0033] S1. Take the cooled density board, cut the density board into a whole sheet or saw the required format size, and sand the surface of the density board;
[0034] S2. Under constant temperature and humidity conditions, adjust the moisture content of the density board and the veneer material, and the adjustment method is: place the density board in a constant temperature and humidity environment for 10 hours, so that the final moisture content of the density board is 10. %, and the internal moisture is evenly distributed, place the dried veneer material in a constant temperature and humidity environment for 10 hours, so that the final moisture content of the veneer material is 7-12%;
[0035] S3. Preheat the density board and the veneer material through the infrared heater, control the ambient temperature to 140°C, send the density board into the infrared heater, and keep the radiation ...
Embodiment 2
[0046] A veneer treatment process for density boards, comprising the following steps:
[0047] S1. Take the cooled density board, cut the density board into a whole sheet or saw the required format size, and sand the surface of the density board;
[0048] S2. Under constant temperature and humidity conditions, adjust the moisture content of the density board and the veneer material, and the adjustment method is: place the density board in a constant temperature and humidity environment for 80 hours, so that the final moisture content of the density board is 6 %, and the internal moisture is evenly distributed, place the dried veneer material in a constant temperature and humidity environment for 60 hours, so that the final moisture content of the veneer material is 7%;
[0049] S3. Preheat the density board and the veneer material through the infrared heater, control the ambient temperature to 200 ° C, send the density board into the infrared heater, and keep the radiation for...
Embodiment 3
[0059] A veneer treatment process for density boards, comprising the following steps:
[0060] S1. Take the cooled density board, cut the density board into a whole sheet or saw the required format size, and sand the surface of the density board;
[0061] S2. Under constant temperature and humidity conditions, adjust the moisture content of the density board and the veneer material, and the adjustment method is: place the density board in a constant temperature and humidity environment for 40 hours, so that the final moisture content of the density board is 8 %, and the internal moisture is evenly distributed, and the dried veneer material is placed in a constant temperature and humidity environment for 30 hours, so that the final moisture content of the veneer material is 9%;
[0062] S3. Preheat the density board and the veneer material through the infrared heater, control the ambient temperature to 18°C, send the density board into the infrared heater, and keep the radiatio...
PUM
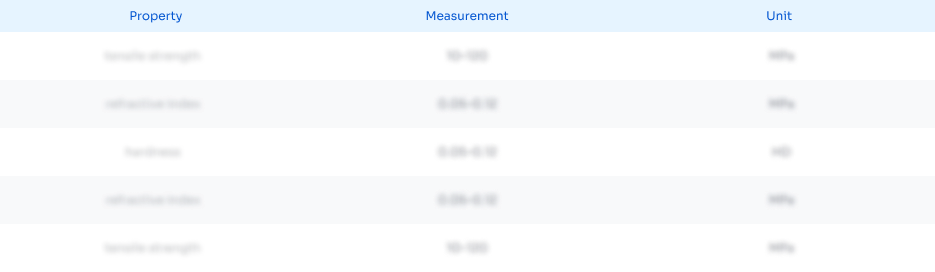
Abstract
Description
Claims
Application Information

- R&D
- Intellectual Property
- Life Sciences
- Materials
- Tech Scout
- Unparalleled Data Quality
- Higher Quality Content
- 60% Fewer Hallucinations
Browse by: Latest US Patents, China's latest patents, Technical Efficacy Thesaurus, Application Domain, Technology Topic, Popular Technical Reports.
© 2025 PatSnap. All rights reserved.Legal|Privacy policy|Modern Slavery Act Transparency Statement|Sitemap|About US| Contact US: help@patsnap.com