Chloromethane synthesis reaction heat gradient comprehensive utilization process
A synthesis reaction and methyl chloride technology, which is applied to the process field of comprehensive utilization of heat in the synthesis reaction of methyl chloride, can solve the problems of not considering the recovery of liquid catalysts, the condensate cannot be fully returned to the kettle for reaction, and the complete vaporization of methanol cannot be guaranteed. Solve the problem of catalyst loss, easy automatic control, and the effect of preventing flying temperature
- Summary
- Abstract
- Description
- Claims
- Application Information
AI Technical Summary
Problems solved by technology
Method used
Image
Examples
Embodiment 1
[0020] Liquid methanol comes from the storage tank at a temperature of 25°C, enters the device area, is divided into two streams of equal volume, and enters the primary vaporizer 2 and the secondary vaporizer 4 respectively. The high-temperature synthesis gas has a temperature of 150°C and is extracted from the methanol synthesis tank 1 and enters the primary vaporizer 2 to exchange heat with methanol. The methanol leaving the primary vaporizer 2 is all vaporized and sent to the methanol feeding section. The synthesis gas exiting the primary vaporizer 2 enters the primary gas-liquid separation tank 3 for separation.
[0021] In the primary gas-liquid separation tank 3 , the synthesis gas exiting the primary gas-liquid separation tank 3 enters the secondary vaporizer 4 . The main components of the liquid phase out of the primary gas-liquid separation tank 3 are hydrochloric acid, by-products, and catalysts entrained by the synthesis gas, which are recycled to the methyl chlori...
Embodiment 2
[0026] Liquid methanol comes from the storage tank at a temperature of 25°C, enters the device area, is divided into two streams of unequal quantities, and enters the primary vaporizer 2 and the secondary vaporizer 4 respectively. The high-temperature synthesis gas is extracted from the methanol synthesis tank 1 and enters the primary vaporizer 2 for heat exchange with methanol. The methanol coming out of the primary vaporizer 2 is completely vaporized at a temperature of 90°C and sent to the methanol feeding section. The synthesis gas exiting the primary vaporizer 2 enters the primary gas-liquid separation tank 3 for separation.
[0027] In the primary gas-liquid separation tank 3 , the synthesis gas exiting the primary gas-liquid separation tank 3 enters the secondary vaporizer 4 . The main components of the liquid phase of the first-stage gas-liquid separation tank 3 are methanol, water, by-products and catalysts entrained by the synthesis gas, which are recycled to the me...
PUM
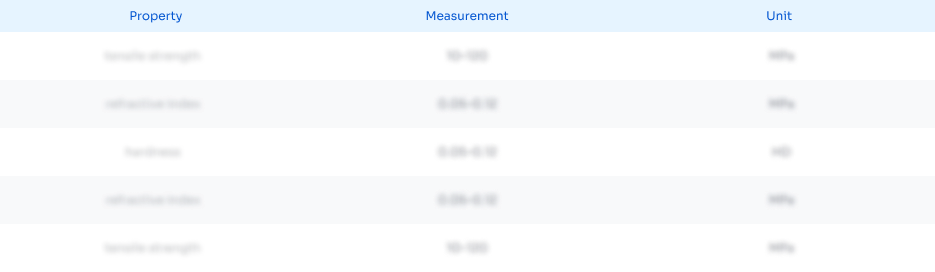
Abstract
Description
Claims
Application Information

- Generate Ideas
- Intellectual Property
- Life Sciences
- Materials
- Tech Scout
- Unparalleled Data Quality
- Higher Quality Content
- 60% Fewer Hallucinations
Browse by: Latest US Patents, China's latest patents, Technical Efficacy Thesaurus, Application Domain, Technology Topic, Popular Technical Reports.
© 2025 PatSnap. All rights reserved.Legal|Privacy policy|Modern Slavery Act Transparency Statement|Sitemap|About US| Contact US: help@patsnap.com