Solvent-free hydrothermal preparation method of carbon material
A technology of carbon materials and hydrothermal method, which is applied in the field of preparation of solvent-free hydrothermal carbon materials, can solve the problems of complicated and time-consuming experimental operations, and achieve the effects of reducing experimental risks, good specific surface area, and saving centrifugal suction and drying
- Summary
- Abstract
- Description
- Claims
- Application Information
AI Technical Summary
Problems solved by technology
Method used
Image
Examples
Embodiment 1
[0026] (1) Take 1g of tannin, 1g of vanillin, and 2g of nano-calcium carbonate and mix them in a mortar. After fully grinding and mixing, add 4-5 drops of 0.5m dilute sulfuric acid to continue grinding, and grind the sample until the surface is wet.
[0027] (2) Transfer the ground sample in step (1) into a 50ml hydrothermal kettle, place it in a vacuum drying oven, and react at 180°C for 12 hours.
[0028] (3) Take out the carbon material precursor in step (2), transfer it into a quartz boat, place it in a tube furnace, and carbonize it in an atmosphere with a nitrogen flow rate of 100 ml / min. The heating rate is 2 °C / min, and the temperature is raised to 900 °C. , After 1.5 hours of heat preservation, cooling treatment.
[0029] (4) The sample obtained in step (3) was ground and pulverized, magnetically stirred with 0.5 m dilute hydrochloric acid for 6 hours, subjected to ultrasonic treatment for 2 hours and then filtered with suction, and the sample was dried in a blast dry...
Embodiment 2
[0032] (1) Take 1g of tannin, 1g of vanillin, and 3g of nano-calcium carbonate and mix them in a mortar. After fully grinding and mixing, add 4-5 drops of 0.5m dilute sulfuric acid to continue grinding, and grind the sample until the surface is wet.
[0033] (2) Transfer the ground sample in step (1) into a 50ml hydrothermal kettle, place it in a vacuum drying oven, and react at 180°C for 11 hours.
[0034] (3) Take out the carbon material precursor in step (2), transfer it into a quartz boat, place it in a tube furnace, and carbonize it in an atmosphere with a nitrogen flow rate of 100 ml / min. The heating rate is 2 °C / min, and the temperature is raised to 900 °C. , After 1.5 hours of heat preservation, cooling treatment.
[0035] (4) The sample obtained in step (3) was ground and pulverized, magnetically stirred with 0.5 m dilute hydrochloric acid for 6 hours, subjected to ultrasonic treatment for 2 hours and then filtered with suction, and the sample was dried in a blast dry...
Embodiment 3
[0038] (1) Take 1g of tannin, 1g of vanillin, and 4g of nano-calcium carbonate and mix them in a mortar. After fully grinding and mixing, add 4-5 drops of 0.5m dilute sulfuric acid to continue grinding, and grind the sample until the surface is wet.
[0039] (2) Transfer the ground sample in step (1) into a 50ml hydrothermal kettle, place it in a vacuum drying oven, and react at 180°C for 10 hours.
[0040] (3) Take out the carbon material precursor in step (2), transfer it into a quartz boat, place it in a tube furnace, and carbonize it in an atmosphere with a nitrogen flow rate of 100 ml / min. The heating rate is 2 °C / min, and the temperature is raised to 900 °C. , After 1.5 hours of heat preservation, cooling treatment.
[0041] (4) The sample obtained in step (3) was ground and pulverized, magnetically stirred with 0.5 m dilute hydrochloric acid for 6 hours, subjected to ultrasonic treatment for 2 hours and then filtered with suction, and the sample was dried in a blast dry...
PUM
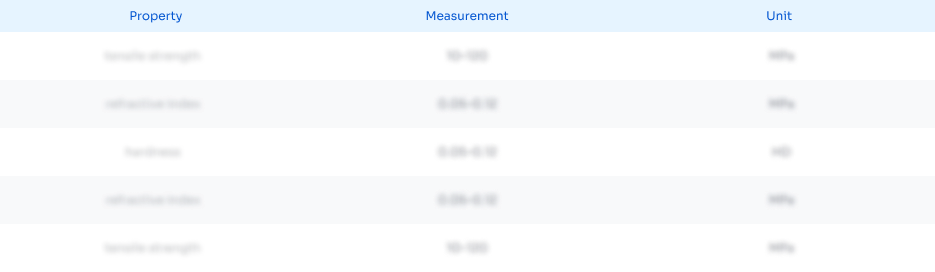
Abstract
Description
Claims
Application Information

- R&D
- Intellectual Property
- Life Sciences
- Materials
- Tech Scout
- Unparalleled Data Quality
- Higher Quality Content
- 60% Fewer Hallucinations
Browse by: Latest US Patents, China's latest patents, Technical Efficacy Thesaurus, Application Domain, Technology Topic, Popular Technical Reports.
© 2025 PatSnap. All rights reserved.Legal|Privacy policy|Modern Slavery Act Transparency Statement|Sitemap|About US| Contact US: help@patsnap.com