Pre-smelting process of electrolytic aluminum liquid
A technology of electrolytic aluminum liquid and pre-smelting, which is applied in the field of aluminum processing, can solve the problems of low pollution, low cost, high pollution, etc., achieve the effects of reducing pressure, reducing secondary oxidation slagging and burning loss, and improving cleanliness
- Summary
- Abstract
- Description
- Claims
- Application Information
AI Technical Summary
Problems solved by technology
Method used
Image
Examples
Embodiment 1
[0066] Embodiment 1: Pre-use 100% electrolytic aluminum liquid to produce 6063 alloy rods for anodic oxidation
[0067] (1) The aluminum capacity of the vacuum bag is 8t each time. After the electrolytic aluminum liquid enters the vacuum bag, the slag content is first tested to be 0.28mm 2 / kg, the hydrogen content is 0.39ml / 100g. After adding 160kg of aluminum-silicon (20%) master alloy, start blowing high-purity argon gas from the microporous air-permeable brick at the bottom of the vacuum bag, with a flow rate of 12L / h and a pressure of 0.6MPa.
[0068] (2) After 15 minutes, after the intermediate alloy is completely melted, a covering agent is placed on the surface of the aluminum melt, and then high-purity argon gas is blown according to the periodic mountain peak, the peak gas flow rate is 5L / h, the peak pressure value is 0.5MPa, the time period is 8min, and the cycle is 3 Second-rate.
[0069] (3) Let stand for another 5 minutes, and remove the covering agent.
[007...
Embodiment 2
[0071] Example 2: Pre-use 100% electrolytic aluminum liquid to produce 5183 alloy rod for high-end welding wire
[0072] (1) The vacuum bag used has an aluminum capacity of 6t each time. After the electrolytic aluminum liquid enters the vacuum bag, the slag content is first tested to be 0.31mm 2 / kg, the hydrogen content is 0.38ml / 100g. After adding 250kg of magnesium ingots, start blowing high-purity argon gas from the microporous air-permeable brick at the bottom of the vacuum bag, with a flow rate of 10L / h and a pressure of 0.6MPa.
[0073] (2) After 15 minutes, after the intermediate alloy is completely melted, arrange a covering agent on the surface of the aluminum melt, and then blow high-purity argon gas according to the periodic mountain peak, the peak gas flow rate is 4L / h, the peak pressure value is 0.5MPa, the time period is 6min, and the cycle is 4 Second-rate.
[0074] (3) Let it stand for another 5 minutes, and remove the covering agent. Sampling test slag conte...
PUM
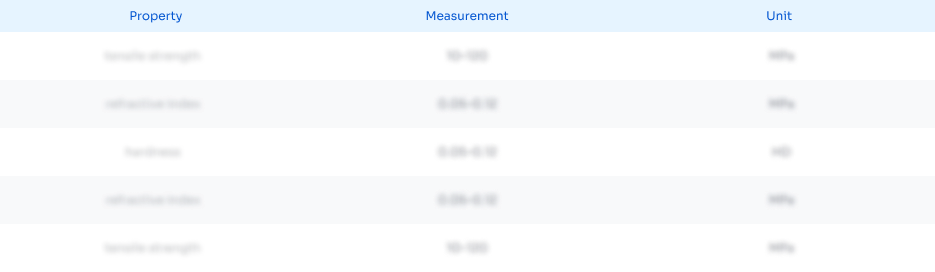
Abstract
Description
Claims
Application Information

- Generate Ideas
- Intellectual Property
- Life Sciences
- Materials
- Tech Scout
- Unparalleled Data Quality
- Higher Quality Content
- 60% Fewer Hallucinations
Browse by: Latest US Patents, China's latest patents, Technical Efficacy Thesaurus, Application Domain, Technology Topic, Popular Technical Reports.
© 2025 PatSnap. All rights reserved.Legal|Privacy policy|Modern Slavery Act Transparency Statement|Sitemap|About US| Contact US: help@patsnap.com