A method for resource utilization of diethyl methylphosphonite high boilers
A technology of diethyl methyl phosphite and alkyl methyl phosphinate, which is applied in the field of resource utilization of diethyl methyl phosphite rectified high boilers, can solve the problem of harsh reaction conditions and safety problems. hidden dangers
- Summary
- Abstract
- Description
- Claims
- Application Information
AI Technical Summary
Problems solved by technology
Method used
Examples
Embodiment 1
[0033] This embodiment provides a method for resource utilization of diethyl methylphosphonite distillation high boilers, said method comprising the following steps:
[0034] (1) Heat 100g of diethyl methylphosphonite rectified high boiler to 40°C, add 26.5g of 2% hydrochloric acid solution (0.015mol) dropwise to the high boiler, after the addition, hydrolyze for 3h, distill Reclaim ethanol to obtain feed liquid A;
[0035] (2) Mix the material liquid A obtained in step (1) with 100g of n-butanol (1.35mol), heat to reflux temperature, and react at 100-110°C. During the reaction, the water produced by the reaction is separated until anhydrous is formed to obtain Feed liquid B;
[0036] (3) Rectify the liquid B obtained in step (2) at -0.098MPa, collect fractions with a fraction temperature of 65-70°C, recover excess n-butanol added during the rectification process, and obtain methylphosphonous acid Mono-n-butyl ester, purity 97.5%, yield 93.0% (based on the sum of diethyl met...
Embodiment 2
[0038] This embodiment provides a method for resource utilization of diethyl methylphosphonite distillation high boilers, said method comprising the following steps:
[0039] (1) Heat 150g of diethyl methylphosphonite rectified high boiler to 80°C, add 40.0g of 3% hydrochloric acid solution (0.033mol) dropwise to the high boiler, after the addition, hydrolyze for 2h, distill Reclaim ethanol to obtain feed liquid A;
[0040] (2) Mix the material liquid A obtained in step (1) with 150g of n-butanol (2.03mol), heat to reflux temperature, and react at 110-120°C. During the reaction, the water produced by the reaction is separated until anhydrous is formed to obtain Feed liquid B;
[0041] (3) Rectify the feed liquid B obtained in step (2) at -0.095MPa, collect fractions with a fraction temperature of 70-75°C, recover excess n-butanol added during the rectification process, and obtain methylphosphonous acid Mono-n-butyl ester with a purity of 98.5% and a yield of 94.5% (based on th...
Embodiment 3
[0043] This embodiment provides a method for resource utilization of diethyl methylphosphonite distillation high boilers, said method comprising the following steps:
[0044] (1) Heat 100 g of diethyl methylphosphonite rectified high boiler to 60° C., 88.3 g of 2% hydrochloric acid solution (0.05 mol) is added dropwise to the high boiler, after the dropwise addition, the hydrolysis reaction is carried out for 0.5 h, Ethanol is reclaimed by distillation to obtain feed liquid A;
[0045] (2) The feed liquid A obtained in step (1) is mixed with 54g n-butanol (0.73mol) and 70g n-butanol (0.95mol) recovered in Example 2, heated to reflux temperature, and reacted at 110~120°C, Separating the water produced by the reaction during the reaction until anhydrous is generated to obtain the feed liquid B;
[0046] (3) Rectify the feed liquid B obtained in step (2) at -0.08MPa, collect the fraction with a fraction temperature of 80-85°C, recover the excessively added n-butanol during the r...
PUM
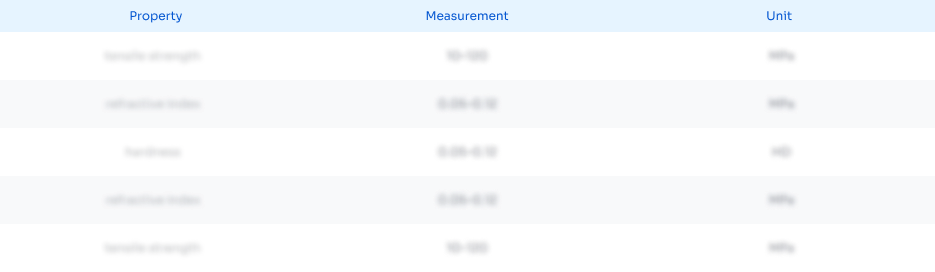
Abstract
Description
Claims
Application Information

- R&D
- Intellectual Property
- Life Sciences
- Materials
- Tech Scout
- Unparalleled Data Quality
- Higher Quality Content
- 60% Fewer Hallucinations
Browse by: Latest US Patents, China's latest patents, Technical Efficacy Thesaurus, Application Domain, Technology Topic, Popular Technical Reports.
© 2025 PatSnap. All rights reserved.Legal|Privacy policy|Modern Slavery Act Transparency Statement|Sitemap|About US| Contact US: help@patsnap.com