Processing method of platinum-rhodium alloy wire with high rhodium content
The technology of a platinum-rhodium alloy and its processing method is applied in the processing field of platinum-rhodium alloy wire with high rhodium content, which can solve the problems of low processing efficiency, increased loss of precious metals, large consumption of auxiliary materials, etc., and achieve good use effect and small loss of precious metals , The effect of stable product quality
- Summary
- Abstract
- Description
- Claims
- Application Information
AI Technical Summary
Problems solved by technology
Method used
Image
Examples
Embodiment 1
[0025] Example 1 High temperature drawing equipment
[0026] like Figure 1-3 As shown, it specifically includes a pay-off barrel 1, a wire release frame 2, a wire tractor 3, a high-temperature furnace 4, a wire take-up barrel 5, a wire take-up frame 6, a wire drawing die 8, an atmosphere cooling pipe 9 and a frame 10 connected in sequence. ;
[0027] The frame 10 is sequentially provided with a pay-off barrel 1, a wire tractor 3, a high-temperature furnace 4 and a take-up barrel 5; the pay-off barrel 1 is provided with a wire release frame 2; wireframe 6;
[0028] A wire drawing die 8 and an atmosphere cooling pipe 9 are also provided between the high temperature furnace 4 and the wire take-up barrel 5; the wire drawing die 8 and the atmosphere cooling pipe 9 are also arranged on the frame 10.
[0029] The wire 7 passes through the pay-off barrel 1 , the wire puller 3 , the high-temperature furnace 4 , the wire drawing die 8 , the atmosphere cooling pipe 9 to the take-up b...
Embodiment 2
[0030] Example 2 PtRh30 wire, target wire diameter φ0.1mm, the steps are as follows:
[0031] (1) Vacuum smelting: Weigh 600.1g of rhodium powder with a purity of SM-Rh99.95% and 1399.9g of pure platinum with a purity of SM-Pt99.95%, put them into a vacuum induction furnace for melting and exhaust, and the vacuum degree is less than 30Pa, after smelting for 1h, cast it into a cylindrical water-cooled copper mold with a diameter of φ22mm under the protection of inert gas;
[0032] (2) Hot forging into bars: Put the ingot obtained in step (1) into an annealing furnace for homogenization annealing and forging. The annealing and forging process is as follows: after holding at 1300°C for 0.5h, take out the hot forging at a processing rate of 30% and then anneal again, repeat the above operation until the ingot is forged to a 10×10mm bar;
[0033] (3) Long rolling and round rolling: use a rolling machine to process the bar obtained in step (2) to φ4.0mm;
[0034] (4) High-temperat...
Embodiment 3
[0036] Example 3 PtRh40 wire material, target wire diameter φ0.5mm, the steps are as follows:
[0037] 1) Vacuum melting: Weigh 800.3g of rhodium powder with a purity of SM-Rh99.95% and 1199.7g of pure platinum with a purity of SM-Pt99.95%, put them into a vacuum induction furnace for melting and exhaust, and the vacuum degree is less than 30Pa , after smelting for 1h, cast it into a cylindrical water-cooled copper mold with a diameter of φ22mm under the protection of an inert gas;
[0038] (2) Hot forging into bars: Put the ingot obtained in step (1) into an annealing furnace for homogenization annealing and forging. The annealing and forging process is as follows: after holding at 1300°C for 0.5h, take out the hot forging at a processing rate of 20% and then anneal again, repeat the above operation until the ingot is forged to a 10×10mm bar;
[0039] (3) Long rolling and round rolling: use a rolling machine to process the bar obtained in step (2) to φ4.0mm;
[0040] (4) Hi...
PUM
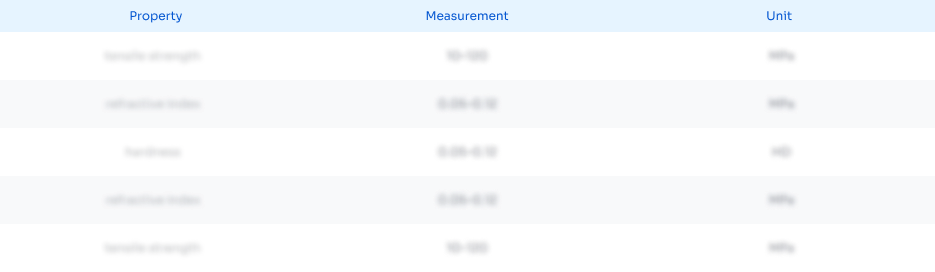
Abstract
Description
Claims
Application Information

- Generate Ideas
- Intellectual Property
- Life Sciences
- Materials
- Tech Scout
- Unparalleled Data Quality
- Higher Quality Content
- 60% Fewer Hallucinations
Browse by: Latest US Patents, China's latest patents, Technical Efficacy Thesaurus, Application Domain, Technology Topic, Popular Technical Reports.
© 2025 PatSnap. All rights reserved.Legal|Privacy policy|Modern Slavery Act Transparency Statement|Sitemap|About US| Contact US: help@patsnap.com