PP material injection molding process and bottle cap prepared by same
A process and raw material technology, which is applied in the field of PP material injection molding process and its prepared bottle caps, can solve the adverse effects of PP plastic products on the tensile properties, the impaired compatibility of PP materials and nucleating agents, and the inconvenience of nucleating agent enhancement Effect and other problems, to improve the mechanical properties of the product, shorten the crystallization cycle, and improve the viscosity
- Summary
- Abstract
- Description
- Claims
- Application Information
AI Technical Summary
Problems solved by technology
Method used
Image
Examples
Embodiment 1
[0038] Embodiment 1: a kind of PP material injection molding process, comprises the following steps:
[0039] Preparation of S1 admixture: Weigh 0.15Kg acetylated distarch phosphate, add 0.3Kg sorbitol nucleating agent, 0.25Kg stearylamide and 0.15Kg microcrystalline paraffin, mix well, heat to 50°C for 3min, to room temperature to prepare the external mixture, pulverize the external mixture with a pulverizer, sieve with a sieve with a pore size of 50 μm, and crush the particles with a particle size greater than 50 μm until the particle size is not greater than 50 μm, and select the particle size not greater than 50 μm Granules to make admixtures.
[0040] S2 Mixing: Weigh 100Kg of PP granules, add the admixture prepared in step S1, and mix evenly to obtain a powder.
[0041] S3 melting: heating the powder prepared in step S2 to 195° C. to obtain a molten liquid.
[0042] S4 injection molding: Heat several standard 3025 mineral water bottle cap molds to 80°C, inject the molt...
Embodiment 2
[0046] The difference between embodiment 2 and embodiment 1 is that embodiment 2 does not add talcum powder, and others are consistent with embodiment 1.
Embodiment 3
[0048] The difference between embodiment 3 and embodiment 1 is that the admixture of embodiment 3 does not undergo the heating pretreatment process, embodiment 3 takes by weighing 0.15Kg acetylated distarch phosphate, adds 0.3Kg sorbitol nucleating agent, 0.25Kg Stearylamide and 0.15Kg microcrystalline paraffin are mixed homogeneously to prepare additive, and others are consistent with Example 1.
PUM
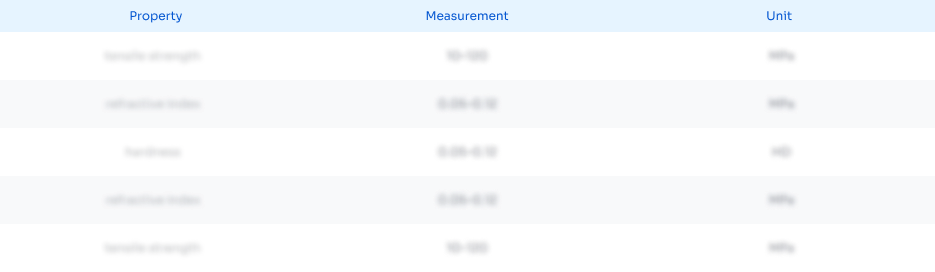
Abstract
Description
Claims
Application Information

- R&D Engineer
- R&D Manager
- IP Professional
- Industry Leading Data Capabilities
- Powerful AI technology
- Patent DNA Extraction
Browse by: Latest US Patents, China's latest patents, Technical Efficacy Thesaurus, Application Domain, Technology Topic, Popular Technical Reports.
© 2024 PatSnap. All rights reserved.Legal|Privacy policy|Modern Slavery Act Transparency Statement|Sitemap|About US| Contact US: help@patsnap.com