Method for deeply removing arsenic, lead, zinc and tin through pyrogenic refining of crude copper
A pyro-refining and blister copper technology, which is applied in the field of deep removal of arsenic and zinc in the pyro-refining of lead, tin and blister copper. Good industrial application prospect and value, better removal effect and wide adaptability of raw materials
- Summary
- Abstract
- Description
- Claims
- Application Information
AI Technical Summary
Problems solved by technology
Method used
Image
Examples
Embodiment 1
[0051] A method for deeply removing arsenic, lead, zinc and tin by pyro-refining of blister copper comprises the following steps:
[0052] (1) Take 0.16g NaHCO respectively 3 , 0.16g CaCO 3 , 0.58g SiO 2 Mix well with 1.1g FeO, prepare particles with a particle size of 2-5mm for use; take 10g blister copper sample and 0.2g waste lead-copper alloy, fill them in an MgO crucible, and place them in a high-purity N 2 Under protection, heat at 1200°C until fully melted.
[0053] (2) Add the slagging agent particles into the molten copper, and inject CO and CO in the laboratory test 2 The mixed gas participates in the slagging reaction of impurities in the material, and the material system (oxygen potential) gradually rises to be the same as the gas phase. In this embodiment, the oxygen partial pressure of the system is controlled to 10 through the combination of gas ratio and temperature (1200°C). -5.5 Atm, keep warm for 2 hours, and control the temperature at 1200°C through a r...
Embodiment 2
[0056] A method for deeply removing arsenic, lead, zinc and tin by pyro-refining of blister copper comprises the following steps:
[0057] (1) Take 0.1g NaHCO respectively 3 , 0.12g CaCO 3 , 0.68g SiO 2 Mix well with 1.1g FeO, and prepare particles with a particle size of 5-8mm for use; take 10g crude copper sample and 0.05g crude lead, fill them in an MgO crucible, and place them in high-purity N 2 Under protection, heat at 1150°C until fully melted.
[0058] (2) Add the slagging agent particles into the molten copper, and pass in CO and CO 2 The mixed gas participates in the slagging reaction of impurities in the material, and the oxygen partial pressure (oxygen potential) of the material system gradually rises to be the same as that of the gas phase. In this embodiment, the oxygen partial pressure of the system is controlled to 10 through the combination of gas ratio and temperature (1150°C). -6.5 atm, heat preservation for 2 hours; after the heat preservation is over, ...
Embodiment 3
[0061] A method for deeply removing arsenic, lead, zinc and tin by pyro-refining of blister copper comprises the following steps:
[0062] (1) Take 0.06g NaHCO respectively 3 , 0.10g CaCO 3 , 0.74g SiO 2 Mix well with 1.1g FeO, and prepare particles with a particle size of 1-4mm for use; take 10g of crude copper sample and 0.3g of waste battery grid, fill them in MgO crucible, and place them in high-purity N 2 Under protection, heat at 1250°C until fully melted.
[0063] (2) Add the slagging agent particles into the molten copper, and pass in CO and CO 2 The mixed gas participates in the slagging reaction of impurities in the material, and the oxygen partial pressure (oxygen potential) of the material system gradually rises to be the same as that of the gas phase. In this embodiment, the oxygen partial pressure of the system is controlled to 10 through the combination of gas ratio and temperature (1250°C). -6 atm, heat preservation for 2 hours; after the heat preservation ...
PUM
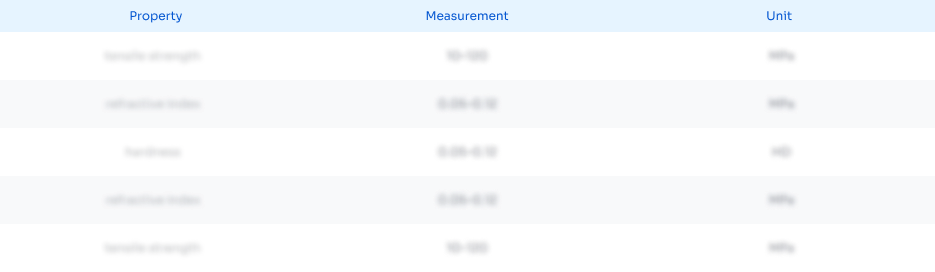
Abstract
Description
Claims
Application Information

- R&D Engineer
- R&D Manager
- IP Professional
- Industry Leading Data Capabilities
- Powerful AI technology
- Patent DNA Extraction
Browse by: Latest US Patents, China's latest patents, Technical Efficacy Thesaurus, Application Domain, Technology Topic, Popular Technical Reports.
© 2024 PatSnap. All rights reserved.Legal|Privacy policy|Modern Slavery Act Transparency Statement|Sitemap|About US| Contact US: help@patsnap.com