Electric arc additive manufacture device using magnetic field and ultrasonic vibration and method
A composite ultrasonic and vibrating arc technology, applied in the field of additive manufacturing, can solve the problems of limited effect of liquid molten pool, uncontrollable arc shape, and molten droplet transition.
- Summary
- Abstract
- Description
- Claims
- Application Information
AI Technical Summary
Problems solved by technology
Method used
Image
Examples
Embodiment
[0049] Take the high-nitrogen steel welding wire with the brand HNS6T2 and a diameter of 1mm, and the 316L stainless steel substrate additive straight wall body with a diameter of 400mm*200mm*10mm as an example. Specific steps are as follows:
[0050] 1. Generate a straight wall additive program in the software and import it into the robot teaching device;
[0051] 2. Polish the 316L stainless steel substrate with a wire brush, remove oxides and other debris, and turn on the shielding gas and welding power;
[0052] 3. Turn on the magnetic control power supply, adjust the current to 2A, and the frequency to 100Hz;
[0053] 4. Turn on the ultrasonic vibration power supply, adjust the vibration frequency to 10kHz, and the amplitude to 100μm;
[0054] 5. Determine the additive process parameters. In this embodiment, the additive mode of CMT+P is selected, the wire feeding speed is 8m / min, the welding speed is 7mm / s, and the shielding gas is 25L / min of Ar1.5%O 2 5%N 2 Ternary ...
PUM
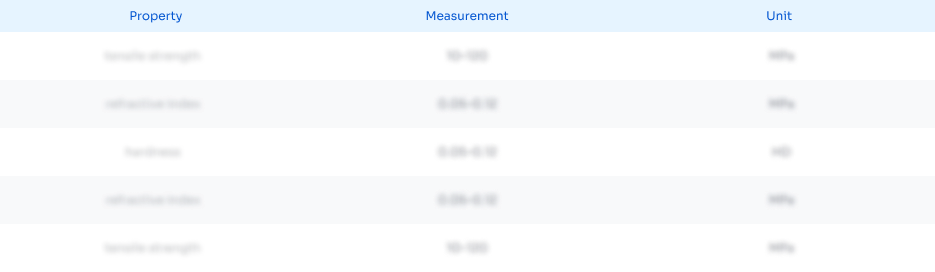
Abstract
Description
Claims
Application Information

- R&D
- Intellectual Property
- Life Sciences
- Materials
- Tech Scout
- Unparalleled Data Quality
- Higher Quality Content
- 60% Fewer Hallucinations
Browse by: Latest US Patents, China's latest patents, Technical Efficacy Thesaurus, Application Domain, Technology Topic, Popular Technical Reports.
© 2025 PatSnap. All rights reserved.Legal|Privacy policy|Modern Slavery Act Transparency Statement|Sitemap|About US| Contact US: help@patsnap.com