Vacuum electroplating UV photo-curing primer and preparation method thereof
A technology of vacuum electroplating and light curing, applied in coatings, primers, polyester coatings, etc., can solve the problem of reducing the coating quality of primers and plastic substrates, the difficulty of bonding between coatings and plastic substrates, and the adhesion of coatings. Poor and other problems
- Summary
- Abstract
- Description
- Claims
- Application Information
AI Technical Summary
Problems solved by technology
Method used
Examples
Embodiment 1
[0039]A vacuum electroplating UV photocuring primer, including 15.0g epoxy acrylic resin, 13.0g polyester acrylate, 12.4g polyurethane acrylic resin, 0.4g adhesion promoter, 20.0g active monomer diluent, 4.0g photoinitiated agent, 35g co-solvent. Among them, the adhesion promoter adopts vinyltrimethoxysilane, the active monomer diluent adopts trimethylolpropane triacrylate, and the photoinitiator takes 1.5g photoinitiator 184 and 2.5g photoinitiator BDK respectively, and the cosolvent Take 3.0g toluene, 1.5g butyl acetate, 25.5g ethyl formate and 5.0g ketone respectively.
[0040] The preparation method of vacuum electroplating UV photocuring primer comprises the steps:
[0041] (1) Feeding: Prepare epoxy acrylic resin, polyester acrylate, polyurethane acrylic resin, vinyl trimethoxy silicon and trimethylolpropane triacrylate according to the formula ratio.
[0042] (2) Dispersion: Disperse the prepared materials at a high speed for 60 minutes at a temperature of 60°C and a ...
Embodiment 2
[0046] A kind of vacuum electroplating UV photocuring primer, this vacuum electroplating UV photocurable primer comprises 10.0g epoxy acrylic resin, 10.0g polyester acrylate, 10.0g polyurethane acrylic resin, 0.3g adhesion promoter, 15.0g active monomer Bulk diluent, 3.0g photoinitiator, 30g co-solvent. Among them, vinyltrimethoxysilane is used as the adhesion promoter, trimethylolpropane triacrylate is used as the active monomer diluent, and 1.1g of photoinitiator 184 and 1.9g of photoinitiator BDK are used as the photoinitiator, and the cosolvent Take 2.5g toluene, 1.3g butyl acetate, 22.0g ethyl formate and 4.2g ketone respectively.
[0047] The difference between this example and Example 1 is only that the weight of the raw materials for the vacuum electroplating UV photocurable primer is different, and the preparation method of the vacuum electroplating UV photocurable primer is the same as that of Example 1.
Embodiment 3
[0049] A kind of vacuum electroplating UV photocuring primer, this vacuum electroplating UV photocurable primer comprises 20.0g epoxy acrylic resin, 15.0g polyester acrylate, 15.0g polyurethane acrylic resin, 0.5g adhesion promoter, 25.0g active monomer Bulk diluent, 5.0g photoinitiator, 40g co-solvent. Among them, vinyltrimethoxysilane is used as the adhesion promoter, trimethylolpropane triacrylate is used as the active monomer diluent, 1.9g of photoinitiator 184 and 3.1g of photoinitiator BDK are used as the photoinitiator, and the cosolvent Take 3.4g of toluene, 1.7g of butyl acetate, 30.0g of ethyl formate, and 5.7g of ketone, respectively.
[0050] The difference between this example and Example 1 is only that the weight of the raw materials for the vacuum electroplating UV photocurable primer is different, and the preparation method of the vacuum electroplating UV photocurable primer is the same as that of Example 1.
PUM
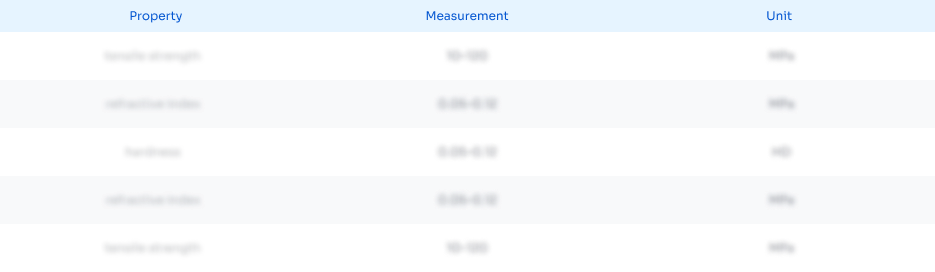
Abstract
Description
Claims
Application Information

- R&D Engineer
- R&D Manager
- IP Professional
- Industry Leading Data Capabilities
- Powerful AI technology
- Patent DNA Extraction
Browse by: Latest US Patents, China's latest patents, Technical Efficacy Thesaurus, Application Domain, Technology Topic, Popular Technical Reports.
© 2024 PatSnap. All rights reserved.Legal|Privacy policy|Modern Slavery Act Transparency Statement|Sitemap|About US| Contact US: help@patsnap.com