Method for preparing self-solidified furan resin for casting by amyl saccharide compound instead of furfuryl alcohol
A furan resin and compound technology, which is applied in casting molding equipment, casting molds, manufacturing tools, etc., can solve the problems of high production costs, achieve the effects of reducing hazards, reducing production costs, and increasing cross-linking points
- Summary
- Abstract
- Description
- Claims
- Application Information
AI Technical Summary
Problems solved by technology
Method used
Examples
Embodiment 1
[0025] Raw material composition:
[0026] Formaldehyde (concentration 37%) 170Kg (17 parts), urea 80Kg (8 parts), furfuryl alcohol 560Kg (56 parts), xylose 100Kg (10 parts).
[0027] The method for producing no-hardening furan resin for foundry by pentose compounds described in this embodiment instead of furfuryl alcohol comprises the following steps:
[0028] (1) Add 17 parts of formaldehyde to the reaction kettle, adjust the pH to 9.2-9.4 with dilute sodium bicarbonate solution to react, then add 10 parts of xylose, and control the temperature at 90-95°C for 1 hour;
[0029] (2) Add 6 parts of urea to the reactor while it is hot to dissolve and stir evenly, then add 18 parts of furfuryl alcohol for reaction, and adjust the pH value of the system to 4.8-5.0 with 20% hydrochloric acid solution, and control the reaction temperature at 90-95°C for reaction 1.5h;
[0030] (3) Add 2 parts of urea to the reactant obtained in step (2) again, adjust the pH value of the material sys...
Embodiment 2
[0033] Raw material composition:
[0034] Formaldehyde (concentration 37%) 150Kg (15 parts), urea 90Kg (9 parts), furfuryl alcohol 550Kg (55 parts), a mixture of arabinose and xylitol 200 Kg (20 parts).
[0035] The method for producing no-hardening furan resin for foundry by pentose compounds described in this embodiment instead of furfuryl alcohol comprises the following steps:
[0036] (1) Add 20 parts of formaldehyde with a concentration of 37% to the reaction kettle, adjust the pH to 9.2-9.4 with dilute sodium hydroxide solution for reaction, then add 20 parts of arabinose, and control the temperature at 85-90°C for 1 hour;
[0037] (2) Add 6 parts of urea to the reactor while it is hot to dissolve and stir evenly, then add 15 parts of furfuryl alcohol for reaction, and adjust the pH value of the system to 2.5-3.5 with 15% oxalic acid solution, and control the reaction temperature at 85-90°C for reaction 1.5h;
[0038] (3) Add 3 parts of urea to the reactant obtained in...
Embodiment 3
[0041] Raw material composition:
[0042] POM solution (concentration 37%) 220Kg (22 parts), urea 60Kg (6 parts), furfuryl alcohol 600Kg (60 parts), xylitol 50 Kg (5 parts).
[0043] The method for producing no-hardening furan resin for foundry by replacing furfuryl alcohol with pentose compounds described in this embodiment is characterized in that it comprises the following steps:
[0044](1) Add 22 parts of polyoxymethylene solution with a concentration of 37% to the reaction kettle, adjust the pH to 9.5-9.7 with a dilute sodium carbonate solution and raise the temperature to 85°C for 1 hour, then add 5 parts of xylitol, and control the temperature at 80- Reaction at 85°C for 1h;
[0045] (2) Add 5 parts of urea to the reactor while it is hot to dissolve and stir evenly, then add 20 parts of furfuryl alcohol for reaction, and adjust the pH value of the system to 4.0-4.5 with 10% sulfuric acid solution, and control the reaction temperature to 80-85°C for reaction 1.5h;
...
PUM
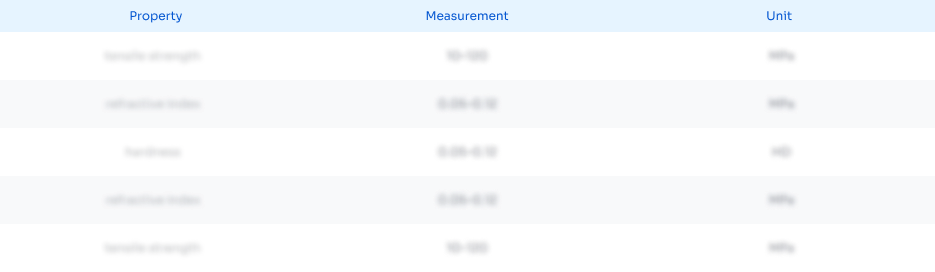
Abstract
Description
Claims
Application Information

- R&D
- Intellectual Property
- Life Sciences
- Materials
- Tech Scout
- Unparalleled Data Quality
- Higher Quality Content
- 60% Fewer Hallucinations
Browse by: Latest US Patents, China's latest patents, Technical Efficacy Thesaurus, Application Domain, Technology Topic, Popular Technical Reports.
© 2025 PatSnap. All rights reserved.Legal|Privacy policy|Modern Slavery Act Transparency Statement|Sitemap|About US| Contact US: help@patsnap.com