High polymer material for surface high-gloss injection molding
A technology of polymer materials and pigments, applied in the field of polymer materials for high-gloss injection molding on the surface, can solve the problems of not fully meeting people's needs, poor gloss, etc., achieve broad market prospects and commercial value, improve brittleness, and reduce costs.
- Summary
- Abstract
- Description
- Claims
- Application Information
AI Technical Summary
Problems solved by technology
Method used
Examples
Embodiment 1
[0024] A high-molecular material for high-gloss surface injection molding, comprising the following components in parts by weight:
[0025] 50 parts of low-density polyethylene, 20 parts of polyethylene oxide, 10 parts of modified glass fiber, 2 parts of light stabilizer, 1 part of antioxidant, and 3 parts of pigment.
[0026] The light stabilizer is 2,6-di-tert-butyl-p-cresol, tetrakis[β-(3,5-di-tert-butyl-4-hydroxyphenyl) propionate] pentaerythritol, thiodipropionate bis Lauryl ester, 1,3,5-trimethyl-2,4,6-tris(3,5-di-tert-butyl-4-hydroxybenzyl)benzene, styrenated phenol, and 20% of β-( A complex of n-octadecyl 3,5-di-tert-butyl-4-hydroxyphenyl)propionate and 80% tris[2.4-di-tert-butylphenyl]phosphite.
[0027] The antioxidant is 2-hydroxyl-4-n-octyloxybenzophenone, 2,2-thiobis(4-tert-octylphenol) n-butylamine nickel salt, and bis(2,2,6, One of 6-tetramethyl-4-piperidinyl) sebacate.
[0028] The preparation method of described modified glass fiber is:
[0029] S1. Weigh ...
Embodiment 2
[0038] A high-molecular material for high-gloss surface injection molding, comprising the following components in parts by weight:
[0039] 80 parts of low-density polyethylene, 40 parts of polyethylene oxide, 15 parts of modified glass fiber, 8 parts of light stabilizer, 10 parts of antioxidant, and 10 parts of pigment.
[0040] The light stabilizer is 2,6-di-tert-butyl-p-cresol, tetrakis[β-(3,5-di-tert-butyl-4-hydroxyphenyl) propionate] pentaerythritol, thiodipropionate bis Lauryl ester, 1,3,5-trimethyl-2,4,6-tris(3,5-di-tert-butyl-4-hydroxybenzyl)benzene, styrenated phenol, and 20% of β-( A complex of n-octadecyl 3,5-di-tert-butyl-4-hydroxyphenyl)propionate and 80% tris[2.4-di-tert-butylphenyl]phosphite.
[0041] The antioxidant is 2-hydroxyl-4-n-octyloxybenzophenone, 2,2-thiobis(4-tert-octylphenol) n-butylamine nickel salt, and bis(2,2,6, One of 6-tetramethyl-4-piperidinyl) sebacate.
[0042] The preparation method of described modified glass fiber is:
[0043] S1. Wei...
PUM
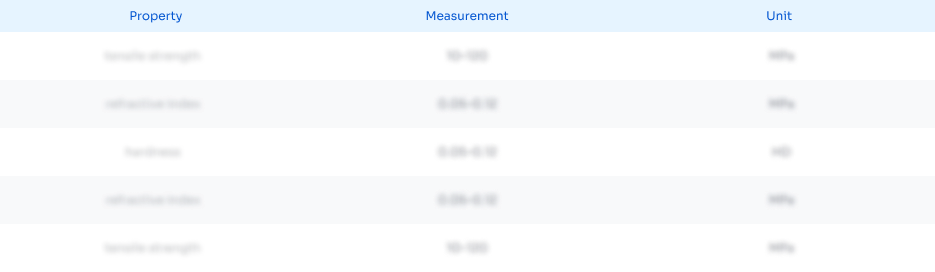
Abstract
Description
Claims
Application Information

- R&D
- Intellectual Property
- Life Sciences
- Materials
- Tech Scout
- Unparalleled Data Quality
- Higher Quality Content
- 60% Fewer Hallucinations
Browse by: Latest US Patents, China's latest patents, Technical Efficacy Thesaurus, Application Domain, Technology Topic, Popular Technical Reports.
© 2025 PatSnap. All rights reserved.Legal|Privacy policy|Modern Slavery Act Transparency Statement|Sitemap|About US| Contact US: help@patsnap.com