Chlorohydrination process epoxide production method for dehydrochlorination of circulating calcium carbonate
An epoxide and dehydrochlorination technology, applied in the fields of organic chemistry, introduction of hydroxyl and halogen preparation, etc., can solve the problems of rising production costs, inability to ensure the balance of chlorine gas in the chlor-alkali industry, and difficulty in the survival of enterprises. Ensure long-term stable operation, raw material route design and intermediate product utilization with advanced and reasonable effects
- Summary
- Abstract
- Description
- Claims
- Application Information
AI Technical Summary
Problems solved by technology
Method used
Image
Examples
Embodiment 1
[0028] The chlorohydrin method epoxide production method of circulating calcium carbonate dehydrochlorination of the present embodiment comprises hypochlorous acid reaction unit 1, chloroalcoholization reaction unit 2, saponification reaction unit 3, epoxide separation unit 4, carbon dioxide recovery unit 5, Calcium carbonate separation unit 6, the specific process is:
[0029] a. Chlorine, water and calcium carbonate from the electrolytic soda plant enter the hypochlorous acid reaction unit 1, in this unit, water and chlorine react to generate hypochlorous acid and hydrogen chloride, and calcium carbonate and hydrogen chloride react to generate calcium chloride, water and carbon dioxide;
[0030] b. The aqueous solution of hypochlorous acid after hydrogen chloride removal from the hydrogen chloride reaction unit 1 enters the chloroalcoholization reaction unit 2 with propylene, and in this unit, propylene reacts with hypochlorous acid to generate the intermediate product chlo...
Embodiment 2
[0036] Embodiment 2 is basically the same as Example 1, except that the raw material to be chloroalcoholized is allyl chloride, and the raw material to be chloroalcoholized is propylene and hypochlorous acid to react to generate the intermediate product dichloropropanol, which reacts with sodium hydroxide to form The target product is epichlorohydrin.
Embodiment 3
[0038] Example 3 is basically the same as Example 1, except that the hypochlorous acid solution leaving the hypochlorous acid reaction unit 1 enters the chloroalcoholation reaction unit 2 after being concentrated.
PUM
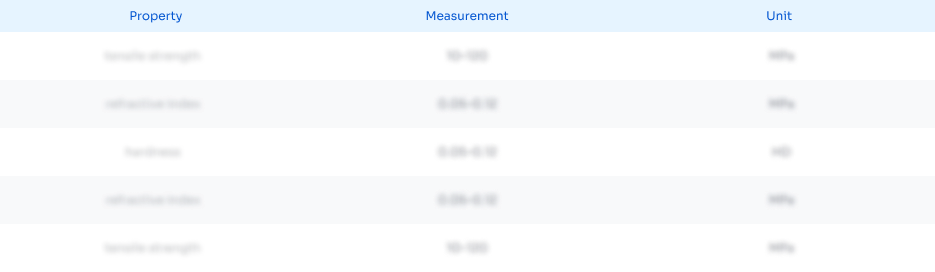
Abstract
Description
Claims
Application Information

- R&D
- Intellectual Property
- Life Sciences
- Materials
- Tech Scout
- Unparalleled Data Quality
- Higher Quality Content
- 60% Fewer Hallucinations
Browse by: Latest US Patents, China's latest patents, Technical Efficacy Thesaurus, Application Domain, Technology Topic, Popular Technical Reports.
© 2025 PatSnap. All rights reserved.Legal|Privacy policy|Modern Slavery Act Transparency Statement|Sitemap|About US| Contact US: help@patsnap.com