Corrosion evaluation method for corrosion-resistant alloy surfacing welding layer of underwater oil and gas facility
A technology of corrosion-resistant alloy and surfacing layer, which is applied in the field of corrosion evaluation of corrosion-resistant alloy surfacing layer of underwater oil and gas facilities, can solve the problems of lack of clear and comprehensive evaluation methods for the corrosion resistance of surfacing layer, and reduce corrosion The effect of risk of failure
- Summary
- Abstract
- Description
- Claims
- Application Information
AI Technical Summary
Problems solved by technology
Method used
Image
Examples
Embodiment
[0119] The corrosion risk of the 625 surfacing layer is explored. The material of the surfacing layer is nickel-based alloy 625, and the base metal is X65.
[0120] Cut the sample along the fusion line, leaving only the upper overlay part.
[0121] The sample was tested for mechanical properties, metallographic structure and hardness. The metallographic sample was made and the metallographic observation was carried out using an optical microscope for the weld part in the middle, and no harmful phase was found. Take 3 points respectively in the weld zone, heat-affected zone and base metal to test the hardness, and the hardness test results meet the requirements of the ISO-15156 standard. The corresponding mechanical performance parameters were obtained by making a tensile sample test, and the results met the requirements of the ISO-15156 standard.
[0122] The long-term corrosion simulation experiment is used for testing, and the experimental environment is specified accordin...
PUM
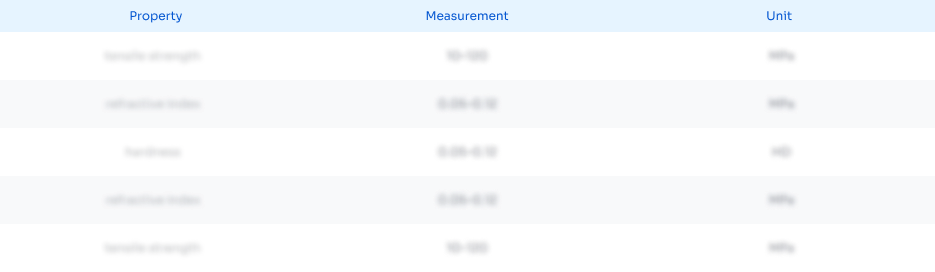
Abstract
Description
Claims
Application Information

- R&D
- Intellectual Property
- Life Sciences
- Materials
- Tech Scout
- Unparalleled Data Quality
- Higher Quality Content
- 60% Fewer Hallucinations
Browse by: Latest US Patents, China's latest patents, Technical Efficacy Thesaurus, Application Domain, Technology Topic, Popular Technical Reports.
© 2025 PatSnap. All rights reserved.Legal|Privacy policy|Modern Slavery Act Transparency Statement|Sitemap|About US| Contact US: help@patsnap.com