A kind of method that formaldehyde is converted into methanol rapidly
A fast, methanol-based technology, applied in chemical instruments and methods, separation methods, preparation of organic compounds, etc., can solve problems such as secondary pollution, limited material adsorption performance, and non-compliance with the green development trend of carbon sequestration and emission reduction. The effect of simple manufacturing process
- Summary
- Abstract
- Description
- Claims
- Application Information
AI Technical Summary
Problems solved by technology
Method used
Image
Examples
Embodiment 1
[0018] Example 1 Effect of activated carbon powder and tris(3-hydroxypropyl)phosphine solid-liquid ratio on formaldehyde conversion
[0019] The activated carbon was ground and passed through a 200-mesh sieve to obtain activated carbon powder. According to the solid-liquid ratio of activated carbon powder and tris(3-hydroxypropyl)phosphine 0.25:1mg / mL, 0.35:1mg / mL, 0.45:1mg / mL, 0.5:1mg / mL, 1.0:1mg / mL, 1.5:1mg / mL mL, 1.55:1 mg / mL, 1.65:1 mg / mL, 1.75:1 mg / mL, respectively, weighed activated carbon powder and tris(3-hydroxypropyl)phosphine, mixed, aged for 12 hours, and air-dried to obtain nine groups of carbon phosphine catalytic materials . Nine groups of carbon phosphine catalytic materials are used as filling materials to fill between the low temperature plasma processor medium baffle and the low pressure electrode plate, and then argon gas is introduced into the polytetrafluoroethylene reaction tank for 5 minutes, and then formaldehyde gas, hydrogen, Argon mixed gas is irr...
Embodiment 2
[0031] Example 2 Influence of the volume ratio of formaldehyde gas, hydrogen gas and argon gas on the conversion of formaldehyde
[0032]The activated carbon was ground and passed through a 300-mesh sieve to obtain activated carbon powder. Activated carbon powder and tris(3-hydroxypropyl)phosphine were weighed according to the solid-liquid ratio of activated carbon powder and tris(3-hydroxypropyl)phosphine at 1.5:1 mg / mL, mixed, aged for 24 hours, and air-dried to obtain carbon phosphine catalyst. Material. The carbon phosphine catalytic material is used as a filling material to fill between the low temperature plasma processor medium baffle and the low pressure electrode, and then argon gas is first introduced into the PTFE reaction tank for 10 minutes, and then formaldehyde gas, hydrogen gas, and argon gas are introduced. The mixed gas is irradiated with low-temperature plasma at the same time, and the gas of the filled carbon phosphine catalytic material is recovered by co...
Embodiment 3
[0037] Example 3 Effect of low temperature plasma irradiation action voltage on formaldehyde conversion
[0038] The activated carbon was ground and passed through a 400-mesh sieve to obtain activated carbon powder. Activated carbon powder and tris(3-hydroxypropyl)phosphine were weighed according to the solid-liquid ratio of activated carbon powder and tris(3-hydroxypropyl)phosphine at 1.5:1 mg / mL, mixed, aged for 36 hours, and air-dried to obtain carbon phosphine catalyst. Material. The carbon phosphine catalytic material is used as a filling material to fill between the low-temperature plasma processor medium baffle and the low-voltage electrode, and then argon gas is first introduced into the polytetrafluoroethylene reaction tank for 15 minutes, followed by formaldehyde gas, hydrogen gas, and argon gas. The mixed gas is irradiated with low-temperature plasma at the same time, and the gas of the filled carbon phosphine catalytic material is recovered by condensation to obta...
PUM
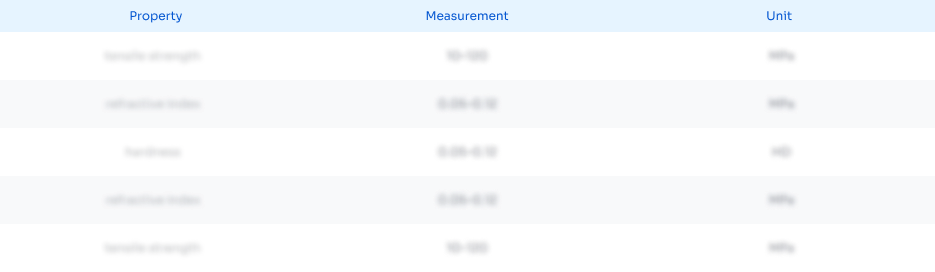
Abstract
Description
Claims
Application Information

- R&D Engineer
- R&D Manager
- IP Professional
- Industry Leading Data Capabilities
- Powerful AI technology
- Patent DNA Extraction
Browse by: Latest US Patents, China's latest patents, Technical Efficacy Thesaurus, Application Domain, Technology Topic, Popular Technical Reports.
© 2024 PatSnap. All rights reserved.Legal|Privacy policy|Modern Slavery Act Transparency Statement|Sitemap|About US| Contact US: help@patsnap.com