A kind of regeneration method and application of deactivated vanadium phosphorus oxygen catalyst
A technology of vanadium phosphorus oxide and catalyst, applied in catalyst regeneration/reactivation, chemical instrument and method, physical/chemical process catalyst, etc. problem, to achieve the effect of recycling
- Summary
- Abstract
- Description
- Claims
- Application Information
AI Technical Summary
Problems solved by technology
Method used
Image
Examples
Embodiment 1
[0029] The deactivated vanadium phosphorus oxygen catalyst was crushed by mechanical grinding, and the catalyst below 60 mesh was sieved, and the temperature was raised to 700°C in a muffle furnace and kept for 5 hours;
[0030] Take 10g of the calcined sample and stir evenly with 80mL of isobutanol, 20mL of benzyl alcohol, and 3.6mL of water, and stir at 135°C for 16h to obtain a light blue precursor solution, filter and separate, wash with ethanol, and dry at 120°C for 12h to obtain light blue colored solid powder;
[0031] 20-40 mesh catalyst particles are obtained through molding, granulation, and sieving processes. After filling, under the atmosphere of butane mixed gas (butane 1.2-1.5%, oxygen 18-20%, nitrogen balance), the space velocity is 2000h -1 After activation at 430°C for 12h, it was evaluated at different temperatures of 400°C, 410°C, 420°C, and 430°C for 24h.
[0032] In this embodiment, the catalytic effect of the regenerated VPO catalyst and the deactivated ...
Embodiment 2
[0034] The deactivated VPO catalyst was crushed by mechanical grinding, and the part below 60 mesh was sieved, and the temperature was raised to 700°C in a muffle furnace and kept for 5 hours;
[0035] Take 10 g of the roasted sample and stir evenly with 80 mL of isobutanol and 20 mL of benzyl alcohol, and stir at 135 ° C for 16 hours. During this period, when the mixed solution gradually changes from dark green to dark gray (after about 10 minutes of reflux stirring), add 3.6 mL of water dropwise. A light blue precursor solution was obtained, separated by filtration, washed with ethanol, and dried at 120°C for 12 hours to obtain a light blue solid powder;
[0036] 20-40 mesh catalyst particles are obtained through molding, granulation, and sieving processes. After filling, in the atmosphere of butane mixed gas (1.2-1.5% butane, 18-20% oxygen, nitrogen balance) atmosphere, the space velocity is 2000h -1 , After activation at 430°C for 12h, evaluate at different temperatures of...
Embodiment 3
[0038] The deactivated VPO catalyst was crushed by mechanical grinding, and the part below 60 mesh was sieved, and the temperature was raised to 700°C in a muffle furnace and kept for 5 hours;
[0039] Take 10 g of the calcined sample and stir evenly with 80 mL of isobutanol and 20 mL of benzyl alcohol, and stir at 135 ° C for 16 hours. During this period, when the mixed solution gradually changes from dark green to dark gray (after about 10 minutes of reflux and stirring), add 3.6 mL of water and 0.5mL phosphoric acid (mass fraction: 85%) to obtain a light blue precursor solution, filter and separate, wash with ethanol, and dry at 120°C for 12h to obtain a light blue solid powder;
[0040] 20-40 mesh catalyst particles are obtained through molding, granulation, and sieving processes. After filling, under the atmosphere of butane mixed gas (butane 1.2-1.5%, oxygen 18-20%, nitrogen balance), the space velocity is 2000h -1After activation at 430°C for 12h, it was evaluated at di...
PUM
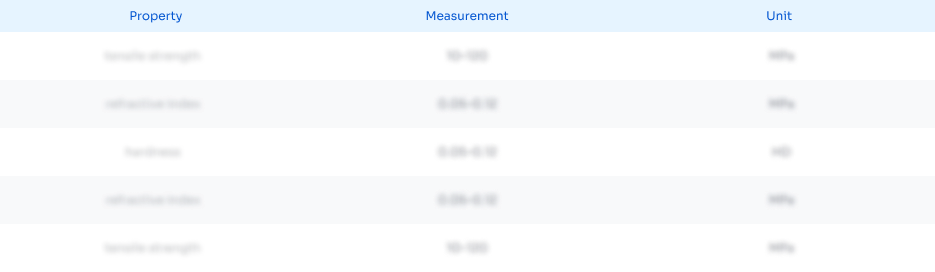
Abstract
Description
Claims
Application Information

- R&D
- Intellectual Property
- Life Sciences
- Materials
- Tech Scout
- Unparalleled Data Quality
- Higher Quality Content
- 60% Fewer Hallucinations
Browse by: Latest US Patents, China's latest patents, Technical Efficacy Thesaurus, Application Domain, Technology Topic, Popular Technical Reports.
© 2025 PatSnap. All rights reserved.Legal|Privacy policy|Modern Slavery Act Transparency Statement|Sitemap|About US| Contact US: help@patsnap.com