Method for calculating instantaneous milling force of carbon fiber reinforced composite material by considering changes of fiber cutting angle and cutting depth
A technology that enhances composite materials and instantaneous milling force. It is applied in the field of mechanical cutting and can solve the problems that the periodical change curve of milling force cannot be obtained, and it has not been considered.
- Summary
- Abstract
- Description
- Claims
- Application Information
AI Technical Summary
Problems solved by technology
Method used
Image
Examples
Embodiment Construction
[0034] The specific implementation of the present invention will be described in detail below in conjunction with the accompanying drawings and technical solutions.
[0035] In this case, it is necessary to predict the milling force of the milling process of the T800 carbon fiber reinforced composite material. The direction angle of the fiber layer is 45°, the thickness of the single-layer plate is 0.2mm, and the composite material unidirectional plate has a total of 20 layers, with a total thickness of 4mm. ;The selected milling cutter is a solid-edge milling cutter with 14 helical edges, the helix angle is 25°, the tool rake angle is 8°, the relief angle is 10°, and the diameter is 10mm; The feeding amount is 1 cm / s, and the rotational speed of the cylindrical milling cutter is 1500 rpm. The specific solution steps are as follows.
[0036] (1). Divide the milling cutter into several microelements along the circumferential direction
[0037] In this scheme, the tool rotatio...
PUM
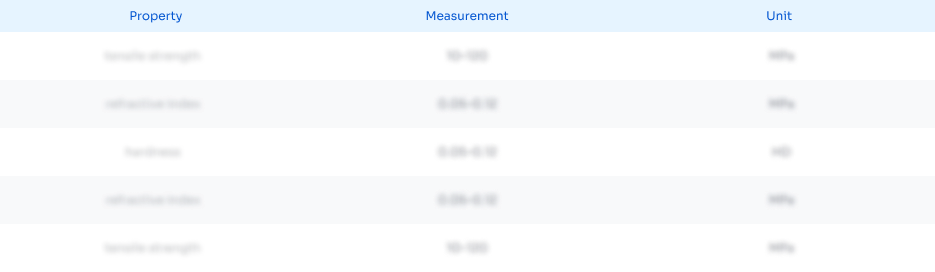
Abstract
Description
Claims
Application Information

- R&D Engineer
- R&D Manager
- IP Professional
- Industry Leading Data Capabilities
- Powerful AI technology
- Patent DNA Extraction
Browse by: Latest US Patents, China's latest patents, Technical Efficacy Thesaurus, Application Domain, Technology Topic, Popular Technical Reports.
© 2024 PatSnap. All rights reserved.Legal|Privacy policy|Modern Slavery Act Transparency Statement|Sitemap|About US| Contact US: help@patsnap.com