Rolling method capable of prolonging service life of roller for conventional hot continuous rolling thin-specification strip steel
A roll life, thin gauge technology, applied in metal rolling and other directions, can solve the problems of high rolling speed, defects, affecting thin gauge, ultra-thin gauge product stability, batch and high-efficiency rolling, etc. Guarantee the effect of the process
- Summary
- Abstract
- Description
- Claims
- Application Information
AI Technical Summary
Problems solved by technology
Method used
Image
Examples
specific Embodiment
[0026] Purpose of the invention: a rolling technology for conventional hot continuous rolling of thin-gauge steel strips. The technology is specifically to control the surface damage caused by the peeling off of the oxide film of the finish rolling work rolls or the uneven wear of the rolls during the rolling process of thin gauges, especially ultra-thin gauges. and rolling stability issues. Innovative, scientific, reasonable and accurate rolling schedule arrangement and flexible process control technology combined with rough rolling mode and intermediate cooling are adopted to control the oxide film shedding of rolls and uneven wear of rolls, so as to achieve conventional hot continuous rolling with thin specifications Consistent high-quality rolling of strip steel.
[0027] The specific technical solutions are as follows:
[0028] 1) Thermal system: the slab is heated by a conventional walking beam heating furnace, the furnace temperature is 1210-1250°C, and the temperature...
Embodiment 1
[0044] This implementation example adopts a 1450mm conventional hot continuous rolling mill to roll a thin specification of 34Km, as follows:
[0045] 1) Steel type for rolling: SAPH440, slab exit temperature 1230-1240°C, soaking time 30min, slab cold loading.
[0046] 2) The rough rolling adopts the "3+3" rolling mode. After rolling, it is coiled by the hot coil box for heat preservation and uniform temperature, and then sent to the finishing rolling unit.
[0047] 3) The starting rolling temperature of the finishing rolling unit is 1030°C, the reverse water spraying and roll gap cooling water of the finished product stand are turned on, the roll gap cooling water of the finished product stand is turned on, and the lubricating rolling is put into use.
[0048] 4) Rolling schedule preparation: front section SAPH440, specification 2.3×1160mm, 19Km; transition section: SPHC, specification 3.0-2.75mm×1160-1200mm; rear section SAPH440, specification 1.8×1180mm, 15Km.
[0049] Imp...
Embodiment 2
[0052] This implementation example adopts a 1450mm conventional hot continuous rolling mill to roll a thin specification of 32Km, as follows:
[0053] 1) Rolled steel grades: SAPH440 and QSTE420, the slab exit temperature is 1230-1250°C, the soaking time is 25min, and the slab is hot delivered and hot charged.
[0054] 2) The rough rolling adopts the "1+5" rolling mode. After rolling, it is coiled by the hot coil box for heat preservation and uniform temperature, and then sent to the finishing rolling unit.
[0055] 3) The starting rolling temperature of the finishing rolling unit is 1030°C, the reverse water spraying and roll gap cooling water of the finished product stand are turned on, the roll gap cooling water of the finished product stand is turned on, and the lubricating rolling is put into use.
[0056] 4) Rolling schedule preparation: front section SAPH440, specification 1.5×1100mm, 20Km; transition section: Q235G, specification 3.0-3.5mm×1250mm; back section QSTE420,...
PUM
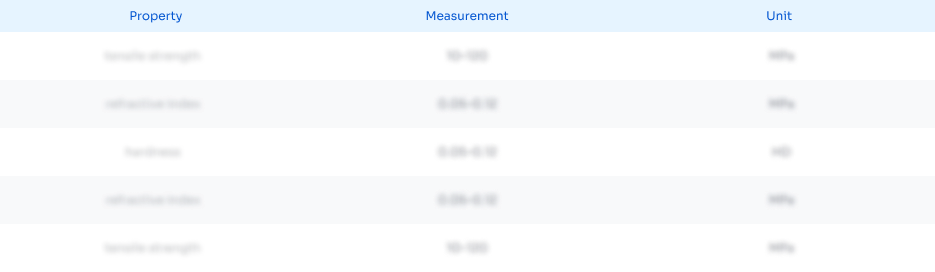
Abstract
Description
Claims
Application Information

- R&D
- Intellectual Property
- Life Sciences
- Materials
- Tech Scout
- Unparalleled Data Quality
- Higher Quality Content
- 60% Fewer Hallucinations
Browse by: Latest US Patents, China's latest patents, Technical Efficacy Thesaurus, Application Domain, Technology Topic, Popular Technical Reports.
© 2025 PatSnap. All rights reserved.Legal|Privacy policy|Modern Slavery Act Transparency Statement|Sitemap|About US| Contact US: help@patsnap.com