A controllable preparation method for particle size classification of nano-vanadium nitride powder
A vanadium nitride powder and particle size technology, which is applied in the field of high melting point nitride powder preparation, can solve problems such as uneven particle size distribution, achieve uniform product particle size distribution, reduce service life, and avoid accumulation effects
- Summary
- Abstract
- Description
- Claims
- Application Information
AI Technical Summary
Problems solved by technology
Method used
Image
Examples
Embodiment 1
[0030] see Figure 1-3 As shown, the dispersion grinding equipment is mainly composed of base plate 1, U-shaped block 2, movable box 4, feed box 12, motor 9 and other components. The structure and installation coordination relationship of each component are as follows:
[0031] The bottom of the U-shaped block 2 is fixed on the top of the bottom plate 1 . The grinding structure 3 is arranged inside the U-shaped block 2 , and the grinding structure 3 is composed of a grinding tank 31 , a rotating shaft 32 , a grinding wheel 35 , a filter plate 33 and a discharge pipe 34 . The both sides of grinding groove 31 are respectively fixed on the both sides of the inner wall of U-shaped block 2, between the both sides of the inner wall of grinding groove 31, rotation is connected with rotating shaft 32, and the outer surface of rotating shaft 32 is fixedly connected with grinding wheel 35, and grinding A filter plate 33 is fixedly connected between both sides of the inner wall of the g...
Embodiment 2
[0041] A controllable preparation method of particle size classification of nano-vanadium nitride powder. In this embodiment, the metal vanadium powder is first surface-treated by dispersing and grinding equipment, and then the vanadium nitride aggregate is prepared by chemical vapor deposition. Finally, the grinding process is carried out again through the dispersion grinding equipment to obtain the finished nano-vanadium nitride powder. The specific steps are:
[0042] 1. The steps for surface treatment of the metal vanadium powder are: adding the metal vanadium powder into the feeding box of the dispersion grinding equipment, and then adding ethanol, sodium fatty acid, and 2-ethylhexyl phosphate mono-2-ethylhexyl ester respectively as Solvent, surface treatment agent and chelating agent; the weight ratio of metal vanadium powder, ethanol, sodium fatty acid, and 2-ethylhexyl phosphate mono-2-ethylhexyl is 1:2:0.1:0.5; processed by dispersing and grinding equipment Modified ...
Embodiment 3
[0046] A controllable preparation method of particle size classification of nano-vanadium nitride powder. In this embodiment, the metal vanadium powder is first surface-treated by dispersing and grinding equipment, and then the vanadium nitride aggregate is prepared by chemical vapor deposition. Finally, the grinding process is carried out again through the dispersion grinding equipment to obtain the finished nano-vanadium nitride powder. The specific steps are:
[0047] 1. The steps for surface treatment of the metal vanadium powder are: adding the metal vanadium powder into the feeding box of the dispersion grinding equipment, and then adding ethanol, sodium fatty acid, and 2-ethylhexyl phosphate mono-2-ethylhexyl ester respectively as Solvent, surface treatment agent and chelating agent; the weight ratio of metal vanadium powder, ethanol, sodium fatty acid, and 2-ethylhexyl phosphate mono-2-ethylhexyl is 1:1:0.5:0.1; processed by dispersing and grinding equipment Modified ...
PUM
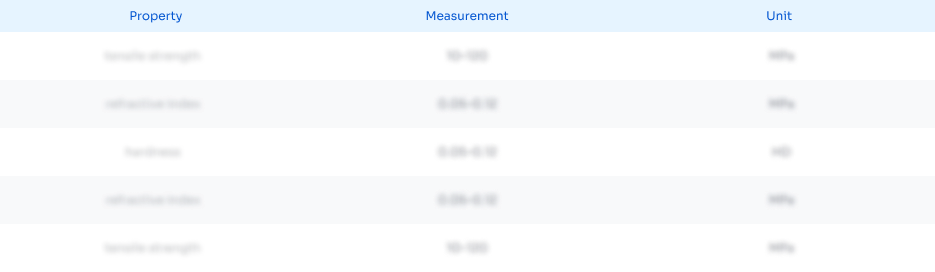
Abstract
Description
Claims
Application Information

- R&D Engineer
- R&D Manager
- IP Professional
- Industry Leading Data Capabilities
- Powerful AI technology
- Patent DNA Extraction
Browse by: Latest US Patents, China's latest patents, Technical Efficacy Thesaurus, Application Domain, Technology Topic, Popular Technical Reports.
© 2024 PatSnap. All rights reserved.Legal|Privacy policy|Modern Slavery Act Transparency Statement|Sitemap|About US| Contact US: help@patsnap.com