Three-stage screw compressor
A screw compressor, compression chamber technology, applied in mechanical equipment, machines/engines, liquid fuel engines, etc., can solve the problems of reduced bearing operating life, damage to the main engine, seizure, rotor wear and deformation, etc., to extend service life, improve Service life, effect of reducing compression ratio and differential pressure
- Summary
- Abstract
- Description
- Claims
- Application Information
AI Technical Summary
Problems solved by technology
Method used
Image
Examples
Embodiment Construction
[0031] See Figure 1 to 10 , A schematic diagram of the plane structure and a three-dimensional structure diagram of a three-stage screw compressor.
[0032] A three-stage screw compressor includes a device body 1, a first compression chamber 7 is opened at the upper end of the device body 1, a water flow groove 6 is opened in the device body 1 relative to the outside of the first compression chamber 7, and the lower end of the device body 1 is fixedly installed A damping base 2 and a heat sink 3 are fixedly installed on the outside of the device main body 1.
[0033] In specific implementation, the inner left and right sides of the shock-absorbing base 2 are fixedly installed with buffer outer rods 4, and the buffer outer rod 4 is movably sleeved with a buffer inner rod 5, so that when the device body 1 generates left and right vibrations, it can overcome The force of the spring presses the inner buffer rod 5 into the outer buffer rod 4, thereby absorbing the shock.
[0034] In sp...
PUM
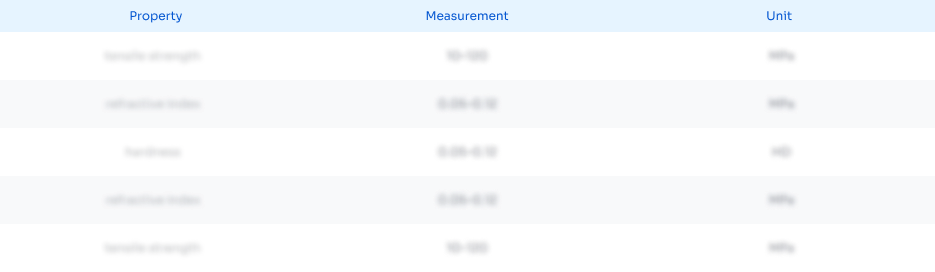
Abstract
Description
Claims
Application Information

- R&D Engineer
- R&D Manager
- IP Professional
- Industry Leading Data Capabilities
- Powerful AI technology
- Patent DNA Extraction
Browse by: Latest US Patents, China's latest patents, Technical Efficacy Thesaurus, Application Domain, Technology Topic, Popular Technical Reports.
© 2024 PatSnap. All rights reserved.Legal|Privacy policy|Modern Slavery Act Transparency Statement|Sitemap|About US| Contact US: help@patsnap.com