Back mold core for anti-falling ceramic tile production and combined back mold core thereof as well as made ceramic tile
An anti-shedding and combined mold technology, applied in the direction of ceramic forming cores, ceramic forming mandrels, etc., can solve the problems of difficulty in applying small-sized ceramic tiles, no implementation equipment and solutions, and high cost of customized components, to simplify the automated production process, The effect of avoiding the decline of tile quality and reducing the risk of card mold
- Summary
- Abstract
- Description
- Claims
- Application Information
AI Technical Summary
Problems solved by technology
Method used
Image
Examples
Embodiment Construction
[0036] The technical solutions of the present invention will be further described in detail below in conjunction with the accompanying drawings and specific embodiments.
[0037] Such as Figure 1-10 , Figure 16 , Figure 17 , Figure 18 As shown, a back mold core for the production of anti-falling tiles, including a mold core panel 1 with a core panel cavity 101 with through holes in the iron parts, a mold core panel 1 with an elastic glue groove hole 203 and a plug screw slide bar guide hole 202 The mold core back plate 2 is integrally molded with wrinkled vulcanizate 601 at the corresponding position of the core panel cavity 101. The core surface vulcanizate 6 covering the front of the core panel 1 is inserted into the cavity 101 of the core panel Embossed insert teeth 3, PU elastic rubber or spring 5 to elastically expand the core face plate 1 and core back plate 2, plug screw 4 for positioning and limiting the movable stroke of the core face plate 1 and core back plat...
PUM
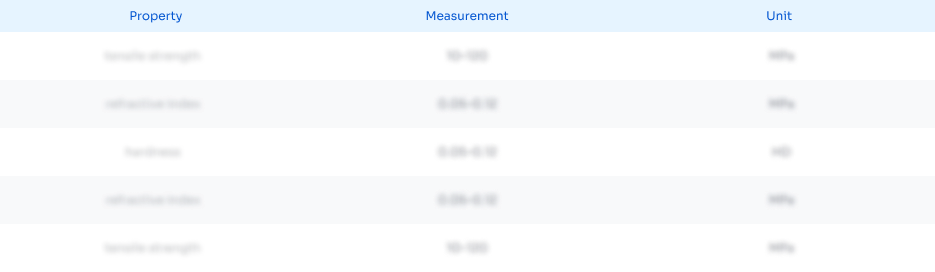
Abstract
Description
Claims
Application Information

- R&D
- Intellectual Property
- Life Sciences
- Materials
- Tech Scout
- Unparalleled Data Quality
- Higher Quality Content
- 60% Fewer Hallucinations
Browse by: Latest US Patents, China's latest patents, Technical Efficacy Thesaurus, Application Domain, Technology Topic, Popular Technical Reports.
© 2025 PatSnap. All rights reserved.Legal|Privacy policy|Modern Slavery Act Transparency Statement|Sitemap|About US| Contact US: help@patsnap.com