Weight-coefficient-free double-motor driving system predictive torque control method
A dual-motor drive and torque prediction technology, which is applied in multiple motor speed/torque control, motor generator control, AC motor control, etc., can solve the problems of system loss increase, phase current distortion, and system zero-sequence current overshoot. Major and other issues
- Summary
- Abstract
- Description
- Claims
- Application Information
AI Technical Summary
Problems solved by technology
Method used
Image
Examples
Embodiment Construction
[0084] The technical solution of the present invention will be specifically described below in conjunction with the accompanying drawings.
[0085] The invention proposes a predictive torque control method for a dual-motor drive system without weight coefficients. The purpose has three aspects: one is to realize the precise control of the torque and stator flux amplitude of the two PMSMs and the effective suppression of the zero-sequence current; the other is to eliminate the weight coefficient of the cost function in the predictive torque control algorithm; the third is to reduce the predicted torque. Calculation amount of the moment control algorithm. According to the six-phase current, DC bus voltage, position angle and other information obtained by system sampling, the expected voltage and zero-sequence voltage expected value of the two PMSMs in the static coordinate system are obtained through the PI regulator, and then through T 6 The inverse transformation of the matri...
PUM
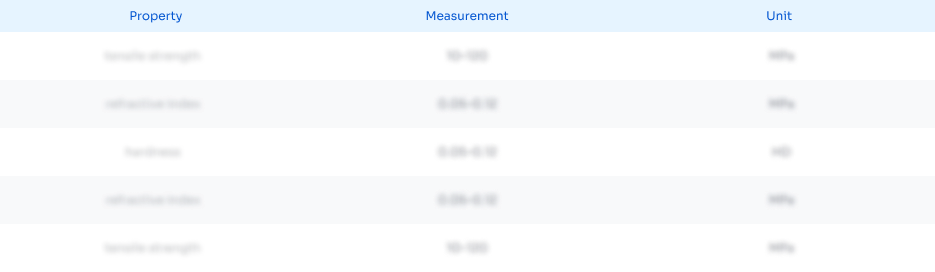
Abstract
Description
Claims
Application Information

- R&D
- Intellectual Property
- Life Sciences
- Materials
- Tech Scout
- Unparalleled Data Quality
- Higher Quality Content
- 60% Fewer Hallucinations
Browse by: Latest US Patents, China's latest patents, Technical Efficacy Thesaurus, Application Domain, Technology Topic, Popular Technical Reports.
© 2025 PatSnap. All rights reserved.Legal|Privacy policy|Modern Slavery Act Transparency Statement|Sitemap|About US| Contact US: help@patsnap.com