Magnesia-carbon wet-process spray coating and application method thereof
A technology of wet spray coating and application method, applied in the field of refractory materials, can solve the problems of short service life, limited construction conditions and high rebound rate, and achieve the effects of reducing the consumption of refractory materials, reducing labor consumption and improving production efficiency
- Summary
- Abstract
- Description
- Claims
- Application Information
AI Technical Summary
Problems solved by technology
Method used
Image
Examples
Embodiment 1
[0025] Fused magnesia 80%Wt (200 mesh, including magnesia for preparing magnesium-carbon composite materials), carbon material 15%Wt (using pitch, graphite powder with a particle size of 325 mesh, and magnesia to prepare magnesia-carbon composite materials), bentonite 2.4 %Wt, water reducer (PC180 polycarboxylate water reducer) 0.2%Wt, sintering agent 2.4%Wt, etc. were pre-mixed to prepare dry mix; coagulant solution (including composite coagulant 10%Wt) was prepared separately. During spraying construction, mix the pre-prepared dry mixture with 4 to 6 times the mass of water as required to prepare a wet material. The wet material has good fluidity and has a storage capacity of more than 2 hours. Under the action of compressed air or booster pump, the wet material is transported to the spray gun through the pipeline, and mixed with the coagulant at the nozzle of the spray gun. The wet material loses its fluidity within 1 minute, and has a high plastic viscosity, which can adhe...
Embodiment 2
[0027] Fused magnesia 90%Wt (200 mesh, including magnesia for preparing magnesium-carbon composite materials), carbon material 3.1%Wt (magnesia-carbon composite materials were prepared using pitch, graphite powder with a particle size of 325 mesh, and magnesia), and bentonite 3.4 %Wt, water reducer (PC180 polycarboxylate water reducer) 0.1%Wt, sintering agent 3.4%Wt, etc. were pre-mixed to prepare dry mix; coagulant solution (including composite coagulant 8%Wt) was prepared separately. During spraying construction, mix the pre-prepared dry mixture with 4 to 6 times the mass of water as required to prepare a wet material. The wet material has good fluidity and has a storage capacity of more than 2 hours. Under the action of compressed air or booster pump, the wet material is transported to the spray gun through the pipeline, and mixed with the coagulant at the nozzle of the spray gun. The wet material loses its fluidity within 1 minute, and has a high plastic viscosity, which c...
PUM
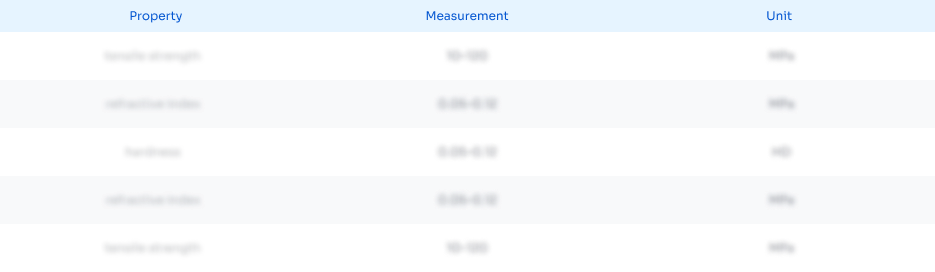
Abstract
Description
Claims
Application Information

- R&D Engineer
- R&D Manager
- IP Professional
- Industry Leading Data Capabilities
- Powerful AI technology
- Patent DNA Extraction
Browse by: Latest US Patents, China's latest patents, Technical Efficacy Thesaurus, Application Domain, Technology Topic, Popular Technical Reports.
© 2024 PatSnap. All rights reserved.Legal|Privacy policy|Modern Slavery Act Transparency Statement|Sitemap|About US| Contact US: help@patsnap.com