Motor rotor punching sheet forming machining process
A technology for forming and processing motor rotors, used in metal processing equipment, manufacturing stator/rotor bodies, manufacturing tools, etc., can solve problems such as increased mass of supporting devices, blockage of worktables, inconvenient feeding, etc., and achieve continuous and stable work. , the effect of preventing accumulation
- Summary
- Abstract
- Description
- Claims
- Application Information
AI Technical Summary
Problems solved by technology
Method used
Image
Examples
Embodiment Construction
[0037] In order to make the technical problems, technical solutions and beneficial effects to be solved by the present invention clearer, the present invention will be further described in detail below in conjunction with the accompanying drawings and embodiments. It should be understood that the specific embodiments described here are only used to explain the present invention, not to limit the present invention.
[0038]Refer to 1-11, a motor rotor punching forming process, which uses a motor rotor punching forming device, the waterproof membrane laying construction device includes a workbench 1, a support plate 2, a driving mechanism 3, The terminal connection block 4, the limit separation mechanism 5, the material receiving mechanism 6 and the stamping terminal 7, the specific method of punching the silicon steel sheet with the above-mentioned motor rotor punching forming processing device is as follows:
[0039] S1. Place the silicon steel sheet: place the silicon steel s...
PUM
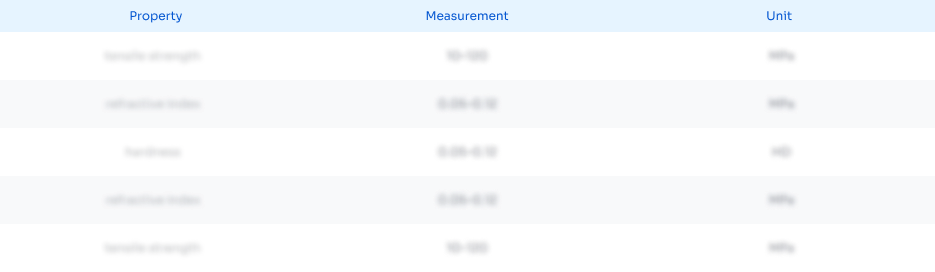
Abstract
Description
Claims
Application Information

- R&D Engineer
- R&D Manager
- IP Professional
- Industry Leading Data Capabilities
- Powerful AI technology
- Patent DNA Extraction
Browse by: Latest US Patents, China's latest patents, Technical Efficacy Thesaurus, Application Domain, Technology Topic, Popular Technical Reports.
© 2024 PatSnap. All rights reserved.Legal|Privacy policy|Modern Slavery Act Transparency Statement|Sitemap|About US| Contact US: help@patsnap.com