Production method of nanometer calcium carbonate for PE direct film blowing
A technology of nano-calcium carbonate and production methods, applied in the direction of calcium carbonate/strontium/barium, chemical instruments and methods, calcium/strontium/barium compounds, etc., can solve the problem of high cost and input cost, difficulty in meeting energy saving and consumption reduction, etc. problems, to achieve the effect of improving mechanical properties, improving melt viscosity, ensuring transparency and gloss
- Summary
- Abstract
- Description
- Claims
- Application Information
AI Technical Summary
Problems solved by technology
Method used
Image
Examples
Embodiment 1
[0041] A kind of production method of the nano-calcium carbonate that is used for PE blown film directly, comprises the steps:
[0042] S1. After the aged calcium hydroxide slurry passes through a suspension separator and a stainless steel screen, the calcium hydroxide slurry is made into a raw slurry with a concentration of 10%, and the temperature of the raw slurry is adjusted to be 30° C.;
[0043] S2. Prepare a solution of crystal form control agent a. The mass percentage of crystal form control agent a is 2.55%, and the concentration is 12.5%. Add it into the carbonization reaction kettle, and pass it under stirring. Carbon dioxide gas reaction for 10.5 minutes;
[0044] S3. After the completion of S2, add the raw slurry of S1 and the crystal form control agent b into the carbonization tower, the mass percentage of the crystal form control agent b is 0.55%, and continue to feed carbon dioxide after stirring for 20 minutes until PH<7.0 The carbonization reaction is comple...
Embodiment 2
[0057] A kind of production method of the nano-calcium carbonate that is used for PE blown film directly, comprises the steps:
[0058] S1. After the aged calcium hydroxide slurry passes through a suspension separator and a stainless steel screen, the calcium hydroxide slurry is made into a raw slurry with a concentration of 8%, and the temperature of the raw slurry is adjusted to be 35° C.;
[0059] S2. Prepare the solution of crystal form control agent a, the mass percentage of crystal form control agent a is 0.1%, the concentration is 20.0%, add it into the carbonization reaction kettle, and pass it under stirring with a concentration of 26% and a temperature <45°C Carbon dioxide gas reaction for 20 minutes;
[0060] S3. After the completion of S2, add the raw slurry of S1 and the crystal form control agent b into the carbonization tower, the mass percentage of the crystal form control agent b is 0.3%, and continue to feed carbon dioxide after stirring for 20 minutes until ...
Embodiment 3
[0073] A kind of production method of the nano-calcium carbonate that is used for PE blown film directly, comprises the steps:
[0074] S1. After the aged calcium hydroxide slurry passes through a suspension separator and a stainless steel screen, the calcium hydroxide slurry is made into a raw slurry with a concentration of 12%, and the temperature of the raw slurry is adjusted to be 25° C.;
[0075] S2. Prepare a solution of crystal form control agent a. The mass percentage of crystal form control agent a is 5.0%, and the concentration is 5.0%. Add it into the carbonization reaction kettle, and feed it with a concentration of 35% and a temperature <45°C under stirring. Carbon dioxide gas reaction for 1min;
[0076] S3. After the completion of S2, add the raw slurry of S1 and the crystal form control agent b into the carbonization tower, the mass percentage of the crystal form control agent b is 0.8%, and continue to feed carbon dioxide after stirring for 20 minutes until PH<...
PUM
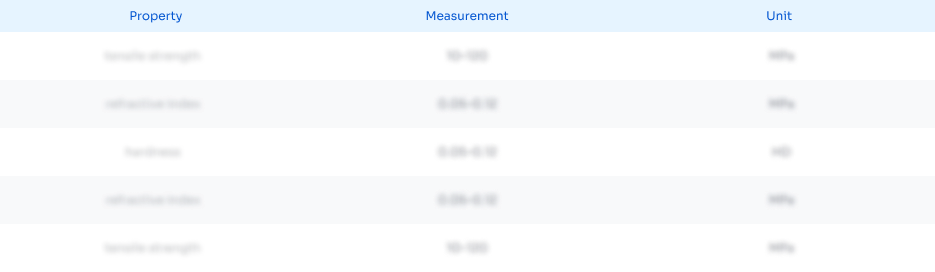
Abstract
Description
Claims
Application Information

- R&D
- Intellectual Property
- Life Sciences
- Materials
- Tech Scout
- Unparalleled Data Quality
- Higher Quality Content
- 60% Fewer Hallucinations
Browse by: Latest US Patents, China's latest patents, Technical Efficacy Thesaurus, Application Domain, Technology Topic, Popular Technical Reports.
© 2025 PatSnap. All rights reserved.Legal|Privacy policy|Modern Slavery Act Transparency Statement|Sitemap|About US| Contact US: help@patsnap.com