Acoustic metamaterial based on impedance matching effect and acoustic device
An acoustic metamaterial and impedance matching technology, applied in the field of acoustics, can solve the problem of significant sound wave reflection, and achieve the effect of improving the impedance mismatch problem
- Summary
- Abstract
- Description
- Claims
- Application Information
AI Technical Summary
Problems solved by technology
Method used
Image
Examples
Embodiment 1
[0056] This embodiment is a simulation embodiment of the acoustic metamaterial 100 . The following will combine Figure 2 to Figure 4 To further illustrate the impedance matching effect of the acoustic metamaterial 100 of the first embodiment. It should be pointed out that in the simulation, the loss of acoustic waves in the hard boundary material is not introduced.
[0057] figure 2 Figure (a) in Figure 1 shows the incident schematic diagram of Embodiment 1, where the arrow indicates the incident direction of the sound wave (ie the x direction). The microstructure 10 is arranged in sequence along the x direction with 3 Class A thin and hard bounded cylinders, 4 Class B thick and hard bounded cylinders, and 3 Class A thin and hard bounded cylinders, and the microstructure 10 is arranged along the y direction with multiple .
[0058] figure 2 Figure (b) in the figure shows the acoustic wave transmission and reflection curves when the microstructure 10 is arranged in 2 la...
Embodiment 2
[0064] This embodiment is an experimental embodiment of the acoustic metamaterial 100 . The following will combine Figure 5 To further illustrate the impedance matching effect of the acoustic metamaterial 100 of the second embodiment.
[0065] Such as Figure 5 As shown, the impedance matching effect of the acoustic metamaterial 100 is further verified by building an acoustic experiment platform.
[0066] Specifically, a speaker is used as a sound source, and a microphone is used as a receiver. The entire experimental platform is sandwiched by two layers of hard boards, similar to a two-dimensional acoustic waveguide, with a height of 30mm. Surrounded by sound-absorbing sponges to reduce the impact of noise. The sample is prepared from resin by 3D printing technology, the structural size of the microstructure 10 is a=30mm, d=3mm, and the number of cycles in the x direction is set to 2, and the length in the y direction is set to 480mm. Different angles of incidence are a...
PUM
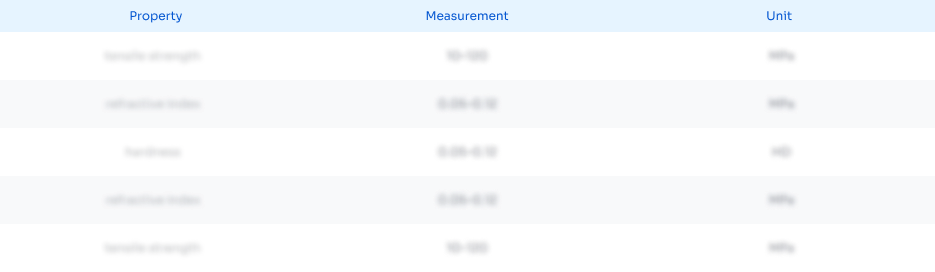
Abstract
Description
Claims
Application Information

- R&D Engineer
- R&D Manager
- IP Professional
- Industry Leading Data Capabilities
- Powerful AI technology
- Patent DNA Extraction
Browse by: Latest US Patents, China's latest patents, Technical Efficacy Thesaurus, Application Domain, Technology Topic, Popular Technical Reports.
© 2024 PatSnap. All rights reserved.Legal|Privacy policy|Modern Slavery Act Transparency Statement|Sitemap|About US| Contact US: help@patsnap.com