Metal gravure plate laser manufacturing method and system
A manufacturing method and technology of gravure printing plate, applied in printing plate preparation, printing, etc., can solve the problems such as seams in plate depth error pattern splicing and affecting manufacturing accuracy, so as to avoid uncontrollable depth error and reduce the occurrence of micro cracks The probability of achieving the effect of connection error compensation
- Summary
- Abstract
- Description
- Claims
- Application Information
AI Technical Summary
Problems solved by technology
Method used
Image
Examples
Embodiment 1
[0060] The metal gravure plate laser manufacturing method provided in this embodiment is to process a pattern with a width of 150mmx70mm on the gravure plate substrate, and its specific implementation process is as follows figure 1 Shown:
[0061] Step 1: Calibrate the corresponding relationship between different depths of single-layer patterns and laser processing parameters;
[0062] Using laser processing equipment to process a single-layer pattern with a size of 40mmx40mm on the gravure plate substrate, test the depth range of single-layer pattern manufacturing, and the corresponding relationship between the depth of single-layer pattern manufacturing and laser processing parameters (power, frequency and other parameters) ;
[0063] Step 2: The pattern structure is layered to obtain a single-layer scanning pattern;
[0064] The designed printing plate structure (150mmx70mm, depth range 5μm-500μm) is layered by layering software, and the uniform layering mode is adopted, ...
Embodiment 2
[0075] The metal gravure plate laser manufacturing method provided in this embodiment is to process a pattern with a format of 1500mmx800mm on the gravure plate substrate. Due to the large format size, sub-regional processing is required. The specific implementation process is as follows figure 2 Shown:
[0076] Step 1: Calibrate the corresponding relationship between different depths of single-layer patterns and laser processing parameters;
[0077] Using laser processing equipment to process a single-layer pattern with a size of 40mmx40mm on the gravure plate substrate, test the depth range of single-layer pattern manufacturing, and the corresponding relationship between the depth of single-layer pattern manufacturing and laser processing parameters (power, frequency and other parameters) ;
[0078] Step 2: Divide the pattern structure of the entire width (1500mmx800mm pattern, depth range 5μm-500μm) into multiple processing areas, and determine the ideal coordinate value ...
PUM
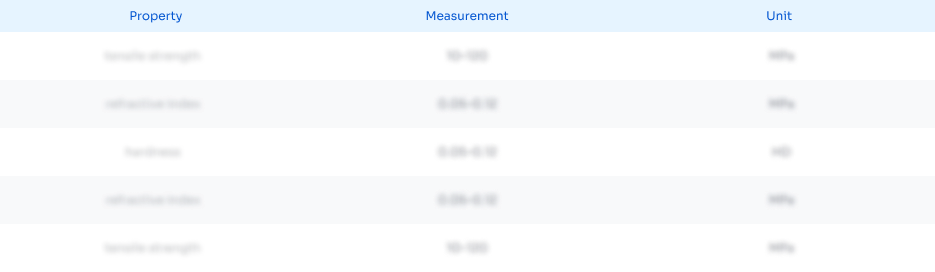
Abstract
Description
Claims
Application Information

- R&D Engineer
- R&D Manager
- IP Professional
- Industry Leading Data Capabilities
- Powerful AI technology
- Patent DNA Extraction
Browse by: Latest US Patents, China's latest patents, Technical Efficacy Thesaurus, Application Domain, Technology Topic, Popular Technical Reports.
© 2024 PatSnap. All rights reserved.Legal|Privacy policy|Modern Slavery Act Transparency Statement|Sitemap|About US| Contact US: help@patsnap.com