Degassing method for Nd-Fe-B permanent magnet before sintered
A permanent magnet and NdFeB technology, which is applied in the degassing field of NdFeB permanent magnets before sintering, can solve the problems of permanent magnets such as reduced magnetic and mechanical properties, unqualified, easy to produce microcracks, etc., to reduce microcracks The probability of improving the pass rate and maintaining the effect of magnetic properties
- Summary
- Abstract
- Description
- Claims
- Application Information
AI Technical Summary
Problems solved by technology
Method used
Image
Examples
Embodiment 1
[0017] Put the first 50 NdFeB permanent magnet blanks into the sintering furnace, and evacuate the sintering furnace until the vacuum degree of the cavity is 2×10 -2 Pa, heated to the primary degassing temperature of 600°C, and at the same time, a certain amount of argon gas with a purity of 99.9% was introduced into the sintering furnace cavity to make the pressure in the sintering furnace cavity 10 Pa, and the temperature was kept at this temperature for 1 hour. First level degassing.
[0018] Vacuum the sintering furnace again until the vacuum degree of the cavity is 2×10 -2 Pa, continue to heat to the secondary degassing temperature of 820 ° C, and at the same time pass a certain amount of argon gas with a purity of 99.9% into the cavity, so that the pressure in the cavity of the sintering furnace is 10 Pa, keep it at this temperature for 1 hour, and carry out Secondary degassing.
[0019] Then, continue heating to 1070°C for sintering, and keep it warm for 3 hours, then...
Embodiment 2
[0021] Put the second 50 NdFeB permanent magnet blanks into the sintering furnace, and vacuum the sintering furnace until the vacuum degree of the cavity is 2×10 -2 Pa, heated to the primary degassing temperature of 600 °C, and at the same time, a certain amount of argon gas with a purity of 99.99% was introduced into the sintering furnace cavity to make the pressure in the sintering furnace cavity 500 Pa, and the temperature was kept at this temperature for 1 hour. First level degassing.
[0022] Vacuum the sintering furnace again until the vacuum degree of the cavity is 2×10 -2 Pa, continue to heat to the secondary degassing temperature of 820 ° C, and at the same time pass a certain amount of argon gas with a purity of 99.99% into the cavity to make the pressure in the cavity of the sintering furnace 500 Pa, keep it warm at this temperature for 1 hour, and carry out the secondary degassing process. level degassing.
[0023] Carry out sintering and tempering according to t...
Embodiment 3
[0025] Put the third part of 50 NdFeB permanent magnet blanks into the sintering furnace, and vacuum the sintering furnace until the vacuum degree of the cavity is 2×10 -2 Pa, heated to the primary degassing temperature of 600 °C, and at the same time, a certain amount of argon gas with a purity of 99.99% was introduced into the sintering furnace cavity to make the pressure in the sintering furnace cavity 1000 Pa, and the temperature was kept at this temperature for 1 hour. First level degassing.
[0026] Vacuum the sintering furnace again until the vacuum degree of the cavity is 2×10 -2 Pa, continue to heat to the secondary degassing temperature of 820 ° C, and at the same time pass a certain amount of argon gas with a purity of 99.99% into the cavity to make the pressure in the cavity of the sintering furnace 1000 Pa, keep the temperature at this temperature for 1 hour, and carry out Secondary degassing.
[0027] Carry out sintering and tempering according to the sintering...
PUM
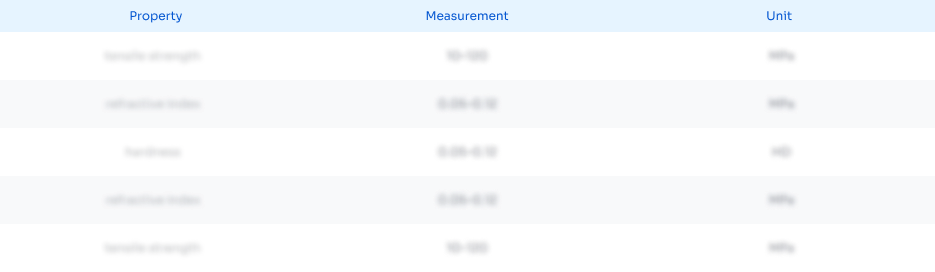
Abstract
Description
Claims
Application Information

- R&D Engineer
- R&D Manager
- IP Professional
- Industry Leading Data Capabilities
- Powerful AI technology
- Patent DNA Extraction
Browse by: Latest US Patents, China's latest patents, Technical Efficacy Thesaurus, Application Domain, Technology Topic, Popular Technical Reports.
© 2024 PatSnap. All rights reserved.Legal|Privacy policy|Modern Slavery Act Transparency Statement|Sitemap|About US| Contact US: help@patsnap.com