Film formation method for controlling the performance of trivalent chromium chemical conversion film on the surface of hot-dip galvanized aluminum alloy coating
A technology of chemical conversion coating and hot-dip galvanizing, which is applied in hot-dip coating process, surface reaction electrolytic coating, metal material coating process, etc. High density and other problems, to achieve the effect of reducing macroscopic roughness, improving uniformity and integrity, and improving corrosion resistance
- Summary
- Abstract
- Description
- Claims
- Application Information
AI Technical Summary
Problems solved by technology
Method used
Image
Examples
Embodiment 1
[0039] The hot-dip galvanized aluminum alloy coating samples were ultrasonically cleaned with acetone for 15 minutes, alcohol for 1 minute, and pure water for 30 seconds, and then the samples were dried at room temperature for later use.
[0040] The prepared hot-dip galvanized aluminum alloy coating sample was used as the cathode, and the platinum sheet electrode was used as the counter electrode anode, and immersed in the trivalent chromium chemical conversion diluent. After immersion for 15s, the cathodic pulse square wave potential was applied to the sample. The potential value of the pulsed square wave potential is -0.05V, the pulse width is 0.1s, the frequency is 5Hz, the duty cycle is 50%, the total pulsed square wave potential is applied for 120s, and the film forming temperature is 30°C.
[0041] The obtained product was washed with pure water for 30 seconds and then dried at room temperature to realize the regulation and control of the properties of the trivalent chr...
Embodiment 2
[0043] The hot-dip galvanized aluminum alloy coating samples were ultrasonically cleaned with acetone for 20 minutes, alcohol for 2 minutes, and pure water for 60 seconds, and then the samples were dried at room temperature for later use.
[0044] The prepared hot-dip galvanized aluminum alloy coating sample was used as the cathode, and the platinum sheet electrode was used as the counter electrode anode, and immersed in the trivalent chromium chemical conversion diluent. After immersion for 20s, the cathodic pulse square wave potential was applied to the sample. The potential value of the pulsed square wave potential is -0.05V, the pulse width is 0.2s, the frequency is 2.5Hz, the duty cycle is 50%, the total pulsed square wave potential is applied for 160s, and the film forming temperature is 40°C.
[0045] The obtained product was washed with pure water for 30 seconds and then dried at room temperature to realize the regulation and control of the properties of the trivalent ...
Embodiment 3
[0047] The hot-dip galvanized aluminum alloy coating samples were ultrasonically cleaned with acetone for 20 minutes, alcohol for 2 minutes, and pure water for 60 seconds, and then the samples were dried at room temperature for later use.
[0048] The prepared hot-dip galvanized aluminum alloy coating sample was used as the cathode, and the platinum sheet electrode was used as the counter electrode anode, and immersed in the trivalent chromium chemical conversion diluent. After immersion for 20s, the cathodic pulse square wave potential was applied to the sample. The potential value of the pulsed square wave potential is -0.10V, the pulse width is 0.2s, the frequency is 2.5Hz, the duty cycle is 50%, the total pulsed square wave potential is applied for 160s, and the film forming temperature is 40°C.
[0049] The obtained product was washed with pure water for 30 seconds and then dried at room temperature to realize the regulation and control of the properties of the trivalent ...
PUM
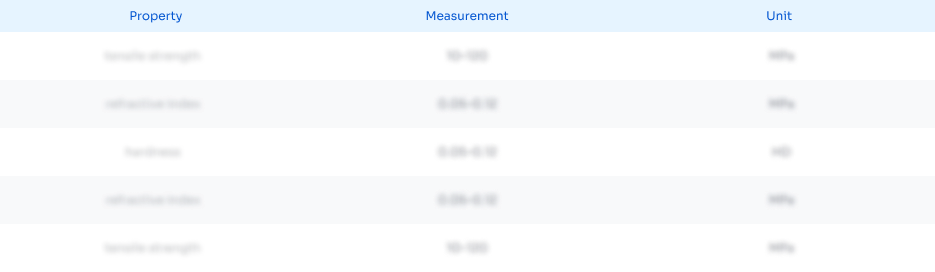
Abstract
Description
Claims
Application Information

- R&D
- Intellectual Property
- Life Sciences
- Materials
- Tech Scout
- Unparalleled Data Quality
- Higher Quality Content
- 60% Fewer Hallucinations
Browse by: Latest US Patents, China's latest patents, Technical Efficacy Thesaurus, Application Domain, Technology Topic, Popular Technical Reports.
© 2025 PatSnap. All rights reserved.Legal|Privacy policy|Modern Slavery Act Transparency Statement|Sitemap|About US| Contact US: help@patsnap.com